Wykorzystanie norm w celu spełnienia minimalnych wymagań bezpieczeństwa
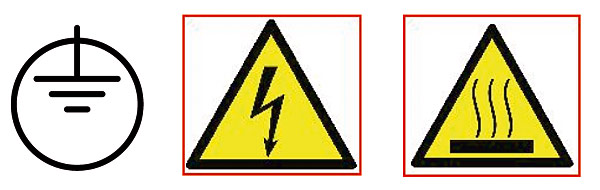
Wspólnota Europejska zdefiniowała dla wspólnego rynku (którego częścią jest obszar RP) wymagania bezpieczeństwa dla maszyn, tworząc dwa filary bezpieczeństwa dla maszyn po raz pierwszy wprowadzanych na rynek WE i maszyn użytkowanych. Ponieważ przepisy prawa w powyższym zakresie, zarówno europejskie, jak i ich krajowe harmonizacje, są formułowane w sposób trudny do bezpośredniego wykorzystania przez projektantów – ustalono, że wsparcie w celu spełnienia wymagań prawnych mogą stanowić normy europejskie, dzięki temu, że określają aktualny stan techniki.
Zasada przedstawiona we wstępie została jednak wprost określona dla filaru bezpieczeństwa produktów nowych, a nie dla maszyn użytkowanych. Jednak, jak zostanie wykazane w dalszej części artykułu, normy techniczne dotyczące bezpieczeństwa maszyn i w tym wypadku mogą być w określony sposób pomocne w spełnieniu wymagań. Wynika to z faktu, iż maszyna po raz pierwszy wprowadzana na rynek jest wdrażana do ruchu i staje się w konsekwencji maszyną użytkowaną, a pozostałe podstawowe czynności, takie jak konserwacja, zmiana lokalizacji (transportowanie) czy inne, są identyczne dla maszyn nowych i używanych.
Oczywiście w praktyce w użytkowaniu znajduje się obecnie wiele maszyn, które zostały wprowadzone po raz pierwszy na rynek przed wejściem Polski w struktury europejskie i niektóre z nich nie muszą posiadać oznaczenia CE. Czyli są to po części maszyny, przy których projektowaniu nie uwzględniano spełnienia zasadniczych wymagań bezpieczeństwa. Maszyny te mogą być oczywiście użytkowane zgodnie z prawem, ale muszą spełniać warunki narzucone dla bezpiecznego stanowiska pracy – czyli sprecyzowane jako minimalne.
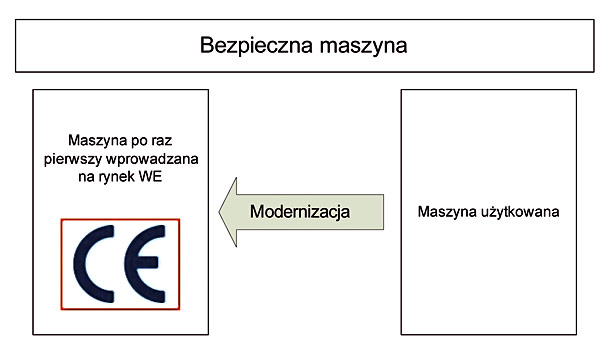
Rys. 1. Dwa filary bezpiecznego produktu w odniesieniu do maszyn
Deklaracja zgodności
W zakresie roli norm, warto przyjrzeć się deklaracji zgodności, która towarzyszy wprowadzeniu na rynek maszyny nowej. Jest to pisemne potwierdzenie przez producenta zachowania zgodności produktu z wymaganiami bezpieczeństwa, które musi precyzować, jakie konkretne akty prawne zostały spełnione. Z tego powodu konieczne jest przytoczenie właściwych rozporządzeń lub ustaw wprowadzających dane dyrektywy odnoszące się do bezpieczeństwa w Polsce. Aby zachować informacje przydatne w obrocie międzynarodowym, trzeba przytoczyć określenia aktów źródłowych, czyli Dyrektyw. Kolejnym ważnym elementem jest wyliczenie podstawowych norm, które wykorzystano w danym przypadku, aby spełnić wymagania bezpieczeństwa. Lista powinna zawierać dokumenty podstawowe, które w powołaniach odnoszą się przecież do ewentualnych innych norm. Ważne, aby były to normy polskie zgodne z europejskimi (PN-EN) związane bezpośrednio z zagadnieniami bezpieczeństwa i zharmonizowane z daną Dyrektywą. Przy czym, jeżeli dla danego rodzaju maszyny istnieje norma szczegółowa typu „C”, to bezwzględnie powinna być ona przytoczona, o ile została wykorzystana. Ponadto ważnym elementem deklaracji zgodności jest wskazanie drogi postępowania. Najczęściej stosuje się procedurę oceny zgodności zwaną modułem „A”, czyli wewnętrzną kontrolę produkcji. W przypadku, gdy maszyna została wymieniona w załączniku nr 2 rozporządzenia o wymaganiach zasadniczych, to konieczne jest podjęcie współpracy z jednostką notyfikowaną, a w ślad za tym ujęcie tego faktu w treści deklaracji. Ponieważ jednostka notyfikowana również z reguły posługuje się adekwatnym zestawem norm zharmonizowanych, logiczne jest, aby tutaj zachodziła zgodność. Deklaracja zgodności wykonana w sposób opisany wyżej wskazuje, że producent przeprowadził procedurę osiągania zgodności z zasadniczymi wymaganiami bezpieczeństwa wykorzystując normy, a więc spełnił przepisy prawa korzystając z zasady domniemania.
Wybrane elementy wymagań minimalnych
Wymagania minimalne obowiązujące pracodawców w Polsce zostały zawarte w rozporządzeniu Ministra Gospodarki [4]. Wymagania te można generalnie podzielić na dwie grupy:
• ogólne – dla maszyn i innych urządzeń technicznych,
• dodatkowe – dla specyficznych maszyn i urządzeń.
Do drugiej grupy zaliczyć należy maszyny mobilne oraz urządzenia przeznaczone do podnoszenia ładunków.
Listy kontrolne
Najczęściej przyjętym sposobem kontroli spełnienia wymagań minimalnych jest technika wykorzystująca listy kontrolne. Przykłady takich list można znaleźć w wielu miejscach w sieci Internet (np. na stronie Państwowej Inspekcji Pracy) oraz w licznych publikacjach. Chociaż można oczywiście posługiwać się listą o charakterze ogólnym, celowe wydaje się sporządzenie list specjalizowanych dla danych – występujących w zakładzie rodzajów maszyn. Listy takie są wówczas z reguły z jednej strony bardziej szczegółowe, a z drugiej lepiej dopasowane do badanych obiektów, co minimalizuje prawdopodobieństwo popełnienia błędów. Ponieważ czynności kontrolne związane z badaniem przez pracodawcę aktualnego stanu spełnienia przez maszynę lub urządzenie wymagań minimalnych bezpieczeństwa powinny być wykonywane wielokrotnie w czasie eksploatacji, warto zadbać o posiadanie list kontrolnych wysokiej jakości.
Kontrole
Maszyny powinny być kontrolowane okresowo, w cyklu nieprzekraczającym 5 lat, lub w przypadku wystąpienia sytuacji specjalnych, do których należą:
• wykonanie zmian w maszynie,
• wystąpienie istotnych dla maszyny zjawisk przyrodniczych (np. powódź),
• wydłużony postój (braku używania) maszyny,
• wystąpienie niebezpiecznych uszkodzeń oraz wypadków przy pracy.
Ponieważ zapisy towarzyszące kontroli należy przechowywać przez okres co najmniej 5 lat do dyspozycji organu kontrolnego, warto zastanowić się, jak powinno wyglądać badanie. Wszystkie czynności związane z bezpieczeństwem zaleca się wykonywać jako z góry zaplanowane, to znaczy należy utworzyć zespół o wystarczających kwalifikacjach. Może on składać się z pracowników danej firmy – o zróżnicowanych specjalnościach oraz obowiązkach. Logiczne wydaje się zaangażowanie pracowników działu utrzymania ruchu, jako specjalistów od środków technicznych bezpieczeństwa, pracowników zarządzających procesem produkcji, jako osób znających specyfikę stanowisk pracy, oraz oczywiście służb BHP, jako specjalistów w zakresie indywidualnych środków ochrony oraz procedur zachowań wymaganych od pracowników w zakresie różnych aspektów bezpieczeństwa. Jeżeli dana firma posiada wdrożony system zarządzania bezpieczeństwem (np. OHSAS 18001 [13]), logiczne jest wdrożenie w tym systemie odpowiedniej procedury i dołączenie do zespołu przedstawicieli działu zarządzania systemem (może to być również zintegrowany system zarządzania, którego podstawę stanowi norma ISO 9001 [14]). Czynności badania mogą być zgodnie z prawem wykonywane przez tak skonstruowany zespół, ponieważ można założyć, że spełniony jest warunek posiadania odpowiednich kwalifikacji.
Ponieważ istnieje szereg specjalizowanych firm zajmujących się doradztwem w zakresie bezpieczeństwa przemysłowego, można również wykonanie tych czynności zlecić na zewnątrz, ale pracownicy danej firmy z definicji dysponują najlepszą wiedzą na temat specyfiki danego zakładu, lepszą od osób z zewnątrz. Osoby z zewnętrznych firm specjalizowanych mają z kolei z reguły większe doświadczenie prowadząc czynności nieustannie w wielu podmiotach gospodarczych, dlatego optymalnym rozwiązaniem wydaje się podjęcie próby utworzenia zespołu mieszanego, złożonego z pracowników i osób zewnętrznych.
Procedura
Kolejnym krokiem jest ustalenie listy maszyn i urządzeń, które mają zostać poddane kontroli i podzielenie ich na grupy, które mogą być badane według takiej samej listy kontrolnej. Następnie należy opracować listy kontrolne dla każdej z grup urządzeń. Listy te powinny zawierać pytania dotyczące kolejno wszystkich wymagań minimalnych właściwych dla danej maszyny (w konkretnym przypadku nie każde wymaganie wymienione w rozporządzeniu musi mieć sens praktyczny). Na każde z pytań można udzielić w ogólnym wypadku jednej i tylko jednej w trzech odpowiedzi: spełnia wymagania (Tak), nie spełnia ich (Nie) lub nie dotyczy (tych odpowiedzi w prawidłowo skonstruowanej liście, dostosowanej do danej maszyny zasadniczo nie powinno być). Przy czym pytania należy w zakresie całej listy formułować w taki sposób, aby w wypadku, gdy maszyna spełnia wszystkie wymagania bezpieczeństwa, wszystkie odpowiedzi konsekwentnie były takie same (np. Tak). Jeżeli zostanie stwierdzone, że jakieś wymaganie nie jest spełnione, należy oddzielnie je wyszczególnić z podaniem przyczyny, terminu przewidywanego usunięcia niezgodności i wskazaniem osoby odpowiedzialnej za usunięcie problemu. Gdy niezgodność zostanie usunięta, należy to komisyjnie potwierdzić i załączyć ewentualne dane związane, np. protokół pomiarów oświetlenia czy hałasu itp.
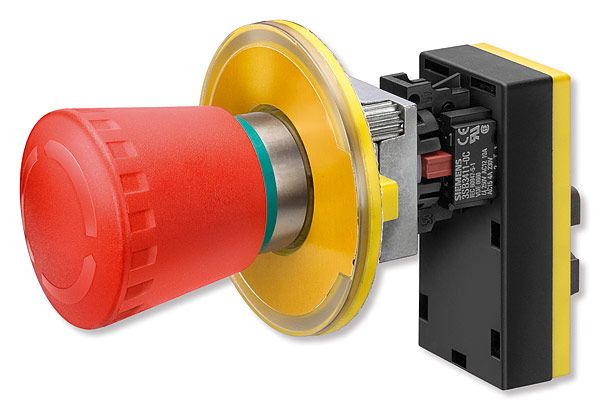
Rys. 2. Element sterowniczy urządzeń zatrzymania awaryjnego
Kryteria
Poza określeniem procedury organizacji badania spełnienia wymagań minimalnych, należy ustalić kryteria, na podstawie których ustalać można spełnienie danego wymagania z listy kontrolnej. Poza ogólną informacją na ten temat zawartą w rozporządzeniu, niezbędne wydaje się ustalenie ścisłych kryteriów technicznych.
Jedną z metod jest, podobnie jak w wypadku określania zgodności z wymaganiami zasadniczymi, posłużenie się normami. W kolejnym rozdziale przedstawione zostaną wybrane przykłady takiego postępowania. Nie należy jednak liczyć, że w normach można znaleźć odpowiedź na wszystkie pytania, ponieważ wymagania minimalne i zasadnicze różnią się, a normy zharmonizowane są opracowywane z myślą o produktach nowych, to znaczy takich, które w zakresie bezpieczeństwa są projektowane zgodnie ze współczesną wiedzą na ten temat. Maszyna wyprodukowana niekiedy znacznie wcześniej może być trudna do dostosowania do wymagań zasadniczych. A właśnie do tego sprowadzałyby się podejmowane czynności w wypadku bezwzględnego wykorzystania całego przewidzianego zestawu norm. Trudno by było zatem rozróżnić wspomniane dwa rodzaje wymagań.
Sens tworzenia dwóch odrębnych filarów bezpieczeństwa produktu w odniesieniu do maszyn polega na zrozumieniu praktycznej różnicy pomiędzy maszyną nową, czyli projektowaną od podstaw (mówiąc najprościej „od pustej kartki papieru”), a istniejącym obiektem poddawanym działaniom dostosowawczym.
Istnieje oczywiście jeszcze jedna droga, polegająca na przeniesieniu w wyniku modernizacji maszyny użytkowanej do filaru produktu nowego, ale w takim wypadku produkt finalny nie powinien być już traktowany jako używany, lecz zakłada się, iż „stara” maszyna stanowi jedynie rodzaj zbioru elementów konstrukcyjnych, które potraktowane jako części składowe wraz z innymi elementami lub urządzeniami służyć mają do wykonania nowej maszyny. W tym scenariuszu produkt finalny jest oczywiście maszyną po raz pierwszy wprowadzaną na rynek, czyli z oznaczeniem CE i deklaracją zgodności. W tym wypadku oczywiście cały proces redukcji ryzyka powinien być realizowany zgodnie z procedurą przewidzianą dla maszyn nowych.
Przykłady zastosowania norm
Jak wspomniano wyżej, rolą norm jest wskazanie projektantom szczegółowych wytycznych, zgodnych z literą prawa zawartego w przepisach – które w wielu wypadkach są zbyt ogólne dla bezpośredniego wykorzystania. Możliwości zastosowania zapisów norm w odniesieniu do tekstów rozporządzeń przedstawiono poniżej, na kilku konkretnych przykładach.
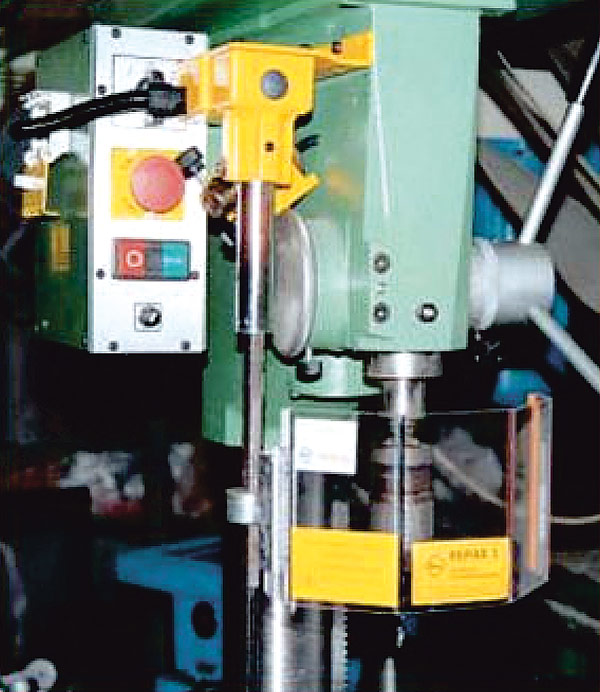
Rys. 3. Osłona wiertarki stołowej
Elementy sterownicze
I tak na przykład w rozporządzeniu [2] jest zapis: „Elementy sterownicze powinny być:
1) Wyraźnie widoczne, rozpoznawalne i, w koniecznych przypadkach, odpowiednio oznakowane;”
A w rozporządzeniu [4] odpowiedni zapis jest następujący:
„1. Elementy sterownicze, które mają wpływ na bezpieczeństwo pracowników, powinny być widoczne i możliwe do zidentyfikowania oraz odpowiednio oznakowane.”
Jak widać, są to w obu wypadkach określenia dość ogólne, chociaż wymagania przez nie stwarzane są jednoznaczne. Ważne jest jednak, w jaki sposób można przełożyć je na konkretne rozwiązanie projektowe. Aby to określić, należy skorzystać z zasady domniemania i wykorzystać normy zharmonizowane, w celu ustalenia niezbędnych parametrów ważnego elementu sterowniczego, którym jest w tym wypadku przycisk zatrzymania awaryjnego. W projekcie tłumaczenia normy PN-EN 60204-1: 2006 znajduje się zapis: „Elementy sterownicze urządzeń zatrzymania awaryjnego powinny być barwy czerwonej. Jeżeli bezpośrednio wokół elementu uruchamiającego znajduje się tło, to powinno być barwy żółtej. Patrz także ISO 13850.”
Jak widać z powyższego przykładu, norma techniczna podaje nie tylko szczegółową wykładnię „odpowiedniego oznakowania” przycisku wyłączenia awaryjnego, ale i odwołuje się w odpowiednim miejscu do innej, bardziej szczegółowej normy [6]. Na szczególną uwagę zasługuje również fakt, iż logiczne jest zastosowanie wykładni danej normy zarówno w wypadku zgodności z wymaganiami zasadniczymi, jak i minimalnymi, ponieważ czerwona barwa przycisku na żółtym tle stanowi zadowalające kryterium warunku widoczności. Minimalizuje również możliwość popełnienia błędu w identyfikacji przycisku o tej ważnej funkcji, przy założeniu, iż czerwona barwa nie może być stosowana do innych przycisków w jego otoczeniu.
Osłony maszyn lub ich części
Innym przykładem może być kwestia dotycząca stosowania osłon maszyn lub ich części. Zarówno przepisy dotyczące maszyn nowych, jak i będących w użytkowaniu przewidują liczne i zbieżne ze sobą warunki nakładane na osłony zarówno stałe, jak i ruchome. Osłony zatem powinny być między innymi: mocne (o trwałej konstrukcji), same nie mogą stanowić źródła zagrożenia, nie mogą być łatwo usuwalne, powinny być usytuowane w odpowiedniej odległości od strefy zagrożenia, co wiąże się również z ich rozmiarem lub możliwością bezpośredniej penetracji (np. wielkość otworów, gęstość siatki itd.), nie powinny ograniczać pola widzenia i ogólnie powinny ograniczać dostęp tylko do niebezpiecznych stref maszyny.
Wymienione wyżej warunki są transponowane przez liczne normy na konkretne parametry osłon, przy czym, analogicznie jak w przypadku rozważań dotyczących przycisku stopu awaryjnego, warunki stawiane osłonom dla maszyn po raz pierwszy wprowadzanych na rynek i będących w użytkowaniu są podobne. W tym wypadku bardzo ważna norma PN-EN ISO 13857 [9] określa szczegółowo wartości oraz metody pomiarowe związane zarówno z planowaniem wielkości osłon, jak ich usytuowania oraz gabaryty ewentualnych otworów. Punktem wyjścia do opracowania danych, które niniejsza norma zawiera, są wymiary antropometryczne oraz parametry ergonomiczne człowieka (typowe dla mieszkańca Europy). Należy oczywiście zakładać, iż są one właściwe zarówno dla maszyn nowych jak i użytkowanych.
Podobne rozważania można przeprowadzić dla oceny prawidłowości umiejscowienia wyposażenia ochronnego ze względu na prędkości zbliżania się części ciała człowieka. Szczegóły techniczne w niniejszej sprawie precyzuje norma PN-EN 999+A1 [10], która również w znacznej mierze jest oparta na danych antropometrycznych i ergonomicznych, a więc w krótkim horyzoncie czasowym niezmiennych. Można zatem przyjąć, że jest ona użyteczna zarówno dla maszyn po raz pierwszy wprowadzanych na rynek, jak i użytkowanych.
W przypadku prowadzenia rozważań nad osłonami należy pamiętać, że spełniają one nie tylko rolę polegającą na ograniczeniu dostępu do stref niebezpiecznych, ale również powinny skutecznie chronić przed emisjami, promieniowaniem, wyrzutami itd. W takim wypadku istotne znaczenie ma ustalenie właściwej ich wytrzymałości lub przepuszczalności. Podstawowe warunki w tym względzie precyzuje norma PN-EN 953 [11]. Podobnie jak uczyniono to wyżej, można w tym zakresie przeprowadzić rozważania, czy poglądy na jakiekolwiek emisje itd. zmieniają się w czasie, a więc czy zasadne jest stosowanie osłon współcześnie uważanych za odpowiednie w maszynach starych. Odpowiedź brzmi oczywiście tak, chociażby z powodu istnienia na rynku oferty licznych osłon gotowych lub prefabrykowanych, wyprodukowanych w zgodności z normami. Poza tym generalna tendencja do zaostrzania z czasem wymagań bezpieczeństwa ma zastosowanie i tutaj, zatem nowszej konstrukcji osłony z pewnością nie będą mniej przydatne.
Zatem przykładowo, warunki narzucone w rozporządzeniu o wymaganiach minimalnych [4] precyzują między innymi, że osłony i oczywiście urządzenia ochronne: „powinny mieć mocną (trwałą) konstrukcję” oraz „nie mogą stwarzać zagrożenia”. W rozporządzeniu [2] wprowadzającym wymagania zasadnicze, odnośne warunki są podobne: „osłony i urządzenia ochronne powinny mieć wytrzymałą konstrukcję” i „nie powinny powodować żadnego dodatkowego ryzyka”. Tak więc nie istnieją przesłanki przeciwdziałające stosowaniu norm jako technicznych materiałów wspierających dobór osłon maszyny użytkowanej.
Należy jednak pamiętać, że już modyfikacja maszyny polegająca na zastąpieniu osłony optoelektronicznymi elementami bezpieczeństwa może prowadzić do zmiany ryzyka (wywoływać konieczność przeprowadzenia nowej oceny ryzyka), a w konsekwencji prowadzić do zakwalifikowania danej modernizacji maszyny jako „głębokiej”.
Generuje to zmianę statusu maszyny do poziomu „jak nowa” i w konsekwencji konieczność zadeklarowania zgodności z wymaganiami zasadniczymi bezpieczeństwa oraz oczywiście nadania oznaczenia CE.
![Rys. 4. Znaki ostrzegawcze wymienione w normie [6]](https://elektrosystemy.pl/wp-content/uploads/uncategorized/2015/11/10/wykorzystanie-norm-w-celu-spelnienia-minimalnych-wymagan-bezpieczenstwa/rys4_SIEMENS_2.jpg)
Rys. 4. Znaki ostrzegawcze wymienione w normie [6]
Normy mogą być również przydatne w zakresie definiowania odpowiedzialności. Dość często w rozważaniach na temat bezpieczeństwa pojawia się problem wykonania dostaw czy usług przez ostatecznego użytkownika maszyny, czyli na własny użytek. Powstaje wówczas pytanie, jak traktować taką sytuację. Otóż na przykład w normie PN-EN 60204-1 [5] można znaleźć definicję dostawcy (3.54) i w uwadze zamieszczonej pod niniejszą definicją przeczytać, że użytkownik może także wystąpić jako dostawca dla samego siebie. Zakładając, że system nie pozostawia luk w zakresie odpowiedzialności za produkt, w przypadku importu na potrzeby własne również wprowadza się produkt na teren wspólnego rynku, a więc istnieje konieczność zadeklarowania zgodności z wymaganiami zasadniczymi. Według tej samej definicji modernizacja wykonana w sposób nie generujący zmiany statusu maszyny na „jak nowa” może być jak najbardziej zrealizowana wewnętrznymi siłami użytkownika. Oczywiście odpowiedzialność w tym wypadku pozostaje przy pracodawcy, który jest jednocześnie użytkownikiem.
Oznakowanie ostrzegawcze
Kolejnym istotnym problemem jest kwestia oznakowania ostrzegawczego maszyny. Jest to ostatni, trzeci etap procesu redukcji ryzyka znanego z normy PN-EN ISO 12100-1 [12]. Oczywiście tak zdefiniowany proces redukcji ryzyka występuje tylko w wymaganiach zasadniczych, ale wymagania minimalne [4] również określają konieczność odpowiedniego oznakowania maszyny: „Maszyny wyposaża się w: […] znaki ostrzegawcze i oznakowania konieczne do zapewnienia bezpieczeństwa pracowników.”
Ponieważ stosowane znaki są dla wszystkich urządzeń takie same, można korzystać z zaleceń normy PN-EN 60204-1 (rys. 4), np. w zakresie:
• oznakowania punktu przyłączenia przewodu ochronnego (punkt 8.2.6 [6]),
• oznakowania zagrożenia porażeniem elektrycznym (punkt 16.2.1 [6]),
• czy oznakowania zagrożenia gorącą powierzchnią (punkt 16.2.2 [6]).
Takie znaki dostępne są również po prostu w handlu.
mgr inż. Marek Trajdos,
Autor jest pracownikiem
firmy T-System Projekt
mgr inż. Wiesław Monkiewicz
Autor jest pracownikiem
firmy Siemens
Artykuł został opracowany
na podstawie materiałów
Klubu Paragraf 34
Bibliografia
[1] Parlament Europejski i Rada, Dyrektywa 98/37/WE z dnia 22 czerwca 1998 r. w sprawie zbliżenia ustawodawstw Państw Członkowskich odnoszących się do maszyn, Dz. U. L 207 z 23.7.1998, str. 1, 1998
[2] Minister Gospodarki, Rozporządzenie z dnia 20 grudnia 2005 r. w sprawie zasadniczych wymagań dla maszyn i elementów bezpieczeństwa, Dz. U. Nr 259, poz. 2170, 2005
[3] Rada Wspólnot Europejskich, Dyrektywa 89/655/EWG z dnia 30 listopada 1989 r. dotycząca minimalnych wymagań w dziedzinie bezpieczeństwa i higieny użytkowania sprzętu roboczego przez pracowników podczas pracy, 1998
[4] Minister Gospodarki, Rozporządzenie z dnia 30 października 2002 r. w sprawie minimalnych wymagań dotyczących bezpieczeństwa i higieny pracy w zakresie użytkowania maszyn przez pracowników podczas pracy, Dz. U. Nr 191, poz. 1596, 2002
[5] Polski Komitet Normalizacyjny, PN-EN 60204-1 Bezpieczeństwo maszyn. Wyposażenie elektryczne maszyn. Część 1: Wymagania ogólne., 2006
[6] Polski Komitet Normalizacyjny, PN-EN ISO 13850 Bezpieczeństwo maszyn – Stop awaryjny – Zasady projektowania., 2006
[7] Trajdos M., Monkiewicz W., Osłony w systemie bezpieczeństwa maszyny, Bezpieczeństwo Przemysłowe. Tom 2., 2008, 117-121
[8] Niechoda Z., Schweitzer T., Normalizacja dobrowolna i bezpieczeństwo, Bezpieczeństwo Przemysłowe. Tom 2., 2008, 9-11
[9] Polski Komitet Normalizacyjny, PN-EN ISO 13857 Bezpieczeństwo maszyn – Odległości bezpieczeństwa uniemożliwiające sięganie kończynami górnymi i dolnymi do stref niebezpiecznych., 2008
[10] Polski Komitet Normalizacyjny, PN-EN 999+A1 Bezpieczeństwo maszyn – Umiejscowienie wyposażenia ochronnego ze względu na prędkości zbliżania części ciała człowieka (oryg.)., 2008
[11] Polski Komitet Normalizacyjny, PN-EN 953 Maszyny – Bezpieczeństwo – Ogólne wymagania dotyczące projektowania i budowy osłon stałych i ruchomych, 1999
[12] Polski Komitet Normalizacyjny, PN-EN ISO 12100-1 Bezpieczeństwo maszyn – Pojęcia podstawowe, ogólne zasady projektowania – Część 1: Podstawowa terminologia, metodologia, 2005
[13] Occupation Health and Safety Assessment Series 18001, 2007
[14] Polski Komitet Normalizacyjn y, PN-EN ISO 9001 Systemy zarządzania jakością – Wymagania, 2009
[15] Ustawa Kodeks Pracy, Dz. U. Nr 21, poz. 94, 1998