Badanie odporności na korozję uziomów pomiedziowanych i ocynkowanych
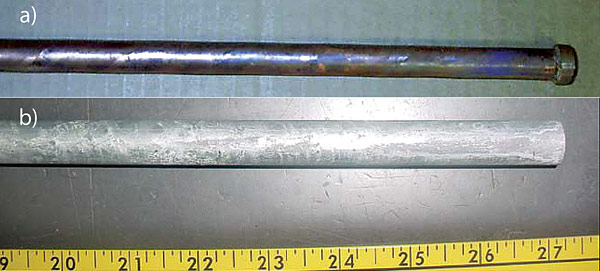
Artykuł przedstawia metodologię badań laboratoryjnych oraz wyniki serii testów korozyjnych przeprowadzonych w kontrolowanych warunkach na grupie wzorców uziomów pomiedziowanych i ocynkowanych, w celu symulacji ich zachowania w glebie. Badania prowadzone były zgodnie z metodologią zawartą w normach europejskich dotyczących systemów uziemiających. Wyniki testu wykazują zdecydowaną różnicę w odporności na korozję obu rodzajów powłok.
Dla wykonania efektywnego i bezpiecznego systemu uziemiającego wykorzystuje się bardzo szeroką gamę uziomów. Odporność uziomów wpływa z kolei na praktyczny okres ich eksploatacji. Pomimo, iż uziomy stalowe pomiedziowane oraz ocynkowane stosowane są od dziesięcioleci, wciąż trwa polemika na temat odporności na korozję każdego z nich – przy zastosowaniu w różnych typach gruntów oraz w różnych warunkach. Celem niniejszego artykułu jest porównanie odporności korozyjnej dwóch najbardziej rozpowszechnionych powłok ochronnych: miedzi oraz cynku.
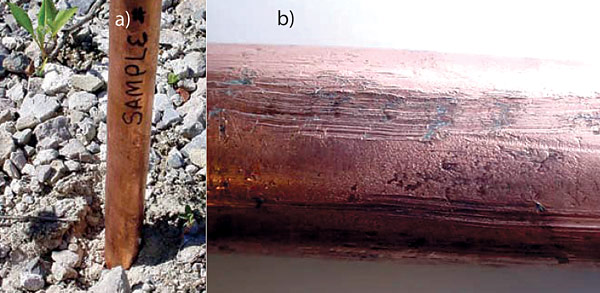
Rys. 1. Pogrążanie uziomu (a), typowe uszkodzenie powłoki przy pogrążaniu uziomów (b)
Stan badań
Przed przystąpieniem do badań sprawdzono w zasobach literatury fachowej dostępność aktualnych opracowań na temat korozyjności elementów pomiedziowanych oraz ocynkowanych. I tak na przykład w badaniach przeprowadzonych w Australii opisano analizę odporności na korozję przewodów ocynkowanych zakopanych w gruncie w różnych warunkach glebowych [1].
W innym z badań na przestrzeni 7 lat sprawdzano stopień korozji złączy ocynkowanych zakopanych w ziemi [2]. Badania wykazały, że połowa powłoki cynku może zdegradować w przeciągu 4 lat. W innym siedmioletnim eksperymencie przeprowadzonym w Szwecji autorzy zanotowali, że 165 µm powłoki cynku na niektórych wzorach ze stali węglowej korodowało z prędkością 22 µm na rok, tzn. powłoka uległaby całkowitej korozji w okresie 7-8 lat [3].
Metodologia badań
Poniżej opisana została eksperymentalna procedura, jakiej użyto dla przeprowadzenia badań porównawczych odporności na korozję powłok miedzianych i cynkowych. W eksperymencie, którego dotyczy artykuł, przyjęto zasadę „najgorszego z wariantów”. Badanie zrealizowano w czterech etapach:
• ocena uszkodzeń, jakie mogą powstać podczas pogrążania uziomów,
• przygotowanie różnych typów próbek, włączając próbki z symulowanymi uszkodzeniami uziomów,
• przeprowadzenie przyspieszonego testu korozyjności w ciągu 28 dni zgodnie z metodologią zawartą w normach europejskich,
• wydobycie wzorców z roztworu korozyjnego po 28 dniach oraz ich inspekcja.

Rys. 2. Generowanie wgnieceń na uziomach (a). Wgniecenia wykonywano według wzoru: 6 wgnieceń o średnicy 0,63 cm i głębokości 0,1-0,2 cm co 2 cm (b)
Uszkodzenia powstające przy pogrążaniu uziomów
W celu oddania realnych, a przy tym ciężkich warunków pogrążania, uziomy stalowe pomiedziowane pogrążano na głębokość około 1 metra w grunt skalisty. Następnie wzorce ostrożnie wydobywano i badano powstałe uszkodzenia. Na rysunku 1 pokazano sposób pogrążania uziomów oraz najczęstszy rodzaj uszkodzenia powłoki.
W żadnym z przypadków nie doszło do uszkodzenia powłoki powodującego odsłonięcie materiału bazowego – rdzenia ze stali węglowej. Podczas prób pogrążania zaobserwowano dwa rodzaje powstałych uszkodzeń:
• długie, ostre zarysowania powierzchni powstałe w wyniku mocnego otarcia o ostry obiekt (długość zarysowań mieściła się w zakresie 5-20 cm),
• krótkie (od 0,1 do 5 cm) płaskie wgniecenia.
Zarówno zarysowania jak i wgięcia pomimo różnic w ich długości i głębokości nie doprowadziły do głębokiej penetracji warstwy ochronnej.
Przygotowanie wzorców uziomów
Przygotowano po dwa egzemplarze 27 różnych rodzajów uziomów – całkowita ilość wzorców wyniosła 54. Każdy uziom przycięto za pomocą pilarki taśmowej do długości 50 cm, eksponując gołą stal na obu końcach wzorca. Końce uziomów zostały wygładzone przy pomocy szlifierki taśmowej. Mniej więcej połowa próbek odwzorowywała oba typy uszkodzeń zaobserwowanych przy pogrążaniu uziomów.
Odwzorowanie uszkodzeń
Przypadek największego uszkodzenia, jakie zanotowano, imitowano wykonując 20-centymetrową rysę na uziomie. Uziom był przytrzymywany przy pomocy podstawki pryzmowej, a prasa generowała uszkodzenia. W trakcie generowania uszkodzeń żaden materiał nie uległ odwarstwieniu. Wgniecenie odwzorowywano precyzyjne, zgodnie z obserwacjami podczas pogrążania uziomu. Imitacja wgnieceń sprawiała więcej problemów ze względu na ich nieregularną charakterystykę. Jednakże udało się uzyskać duży stopień podobieństwa uszkodzeń poprzez zastosowanie prasy hydraulicznej. Na każdym imitującym uszkodzenie wzorcu wytłoczono sześć wgnieceń co 2 cm. Typowa średnica wgniecenia wynosiła 0,63 cm, a głębokość ingerencji wynosiła od 0,1 do 0,2 cm. Proces wgniatania został zilustrowany na rysunku 2.
Pomiary przed testem
Przed przystąpieniem do przyspieszonego testu korozyjności uziomów zmierzono wagę, średnicę, długość oraz rezystancję dla każdej próbki. Dane te zanotowano dla porównania z wynikami po przeprowadzeniu testu. Ważenie każdego wzorca odbywało się przy pomocy skalibrowanego urządzenia Toploader Balnce6X-800 z dokładnością do 0,001 grama, po uprzednim oczyszczeniu wzorca miękką szmatką. Średnicę uziomów mierzono w trzech punktach: przy obu końcach oraz pośrodku. Do pomiaru z dokładnością do 10 mikrometrów użyto skalibrowanego miernika Mitutoyo Absolute Digimatic Calipers. Długość wzorców mierzono z dokładnością do 0,5 mm. Rezystancję każdego wzorca zbadano przy pomocy cyfrowego mikroomometra DRM-40 wzdłuż trzech różnych 100 -milimetrowych odcinków (blisko końców i pośrodku) z dokładnością do 0,01 µW.
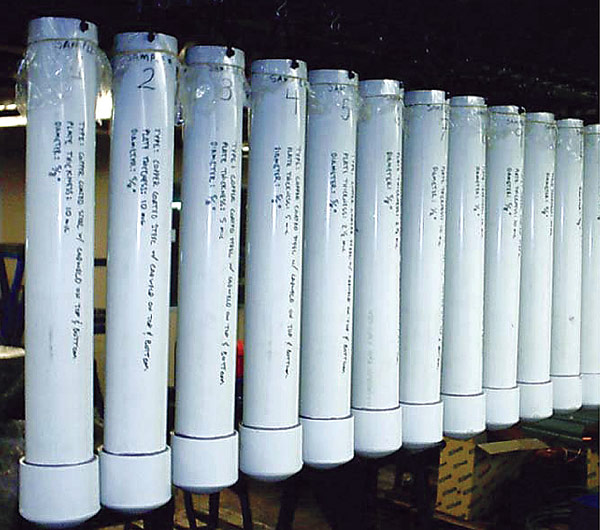
Rys. 3. Wzorce uziomów zawieszone w tubach PVC z roztworem
Przyspieszony test korozyjny
Przyspieszony test korozyjny był przeprowadzony na wzorcach zgodnie z metodologią zawartą w EN50164-2. Każdą próbkę umieszczono w oddzielnej czystej tubie z PVC utworzonej z 50 cm odcinka rury zakończonej pokrywką. Średnica tuby z PVC wynosiła 5 cm, tak więc ilość roztworu 10-krotnie przewyższała objętość wzorca. Każdy wzorzec uziomu umieszczono w tubie, a potem całkowicie zalano niemieszanym, oczyszczonym roztworem wody z chlorkiem wapnia (CaCl2) oraz siarczkiem sody (Na2SO4). Skład chemiczny roztworu był następujący: 1 litr H2O, 650 mg CaCl2, 1500 mg Na2SO4. Temperatura roztworu wynosiła 20oC, a pH mieściło się w zakresie 5-9. Otwarty koniec każdej z tub został zamknięty przy pomocy folii i gumki w celu ograniczenia wyparowywania roztworu. Po zanurzeniu wzorce pozostawiono w roztworze, a tuby zawieszono w pomieszczeniu o kontrolowanej temperaturze ustawionej na 20oC na 28 dni.
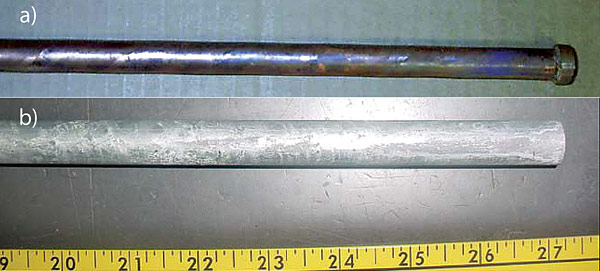
Rys. 4. Typowy wzorzec uziomu stalowego pomiedziowanego (a) oraz ocynkowanego (b) po 28 dniowym przyśpieszonym teście korozyjnym
Wydobycie oraz pomiary wzorców
Pod koniec 28 dnia badań wszystkie wzorce wydobyto z roztworu, wymyto oraz wysuszono. Procedura mycia i suszenia wzorców przebiegała w taki sposób, aby zabezpieczyć neutralność wyników. Wzorce myto pod bieżącą wodą kranową, płukano w wodzie zdejonizowanej, częściowo suszono miękką szmatką i na koniec suszono przy pomocy palnika. Następnie każdy wzorzec umieszczono w plastikowej, zamykanej torebce przed dokonaniem końcowych pomiarów. Pomiary końcowe przeprowadzono w ten sam sposób, co początkowe, tzn. zbadano wagę, średnicę, długość oraz rezystancję każdego wzorca.
Wyniki
Tabela 1 zawiera rezultaty przeprowadzonych badań na odporność korozyjną 27 różnych typów uziomów (po dwa wzorce z każdego typu) zgodnie z procedurą opisaną wcześniej. Rysunek 4 pokazuje typowy uziom stalowy pomiedziowany oraz stalowy ocynkowany po wyjęciu z roztworu. Zgodnie z normą EN50164-2 uziomy po przejściu badania powinny spełniać następujące wymagania:
• opór elektryczny mierzony na odcinku 100 mm długości po przeprowadzeniu testu środowiskowego nie powinien przekraczać wartości początkowej przed poddaniem testowi więcej niż o 50%,
• materiał bazowy nie może nosić śladów korozji,
• wzorce powinny być gładkie bez ostrych powierzchni.
Pod względem zmiany oporności wszystkie wzorce spełniły wymagania normy. Średni wzrost rezystancji wyniósł około 5%. W przypadku pozostałych kryteriów żaden ze wzorców nie wykazywał śladów korozji materiału bazowego (stali węglowej) lub istnienia ostrych powierzchni. Tak więc wszystkie 54 wzorce spełniły wymagania opisane w normie.
Porównanie właściwości
Natomiast bliższa analiza wyników testów uwidoczniła znaczne różnice w poziomie odporności na korozję między uziomami pomiedziowanymi i ocynkowanymi. Średnia utrata wagi dla wszystkich uziomów pomiedziowanych wynosiła 144 mg, natomiast w przypadku uziomów ocynkowanych było to 213 mg. Średnia utrata wagi dla gołych uziomów stalowych wynosiła 224 mg – nieznacznie więcej niż w przypadku uziomów ocynkowanych. Świadczy to o tym, że powłoka cynkowa na uziomach stalowych ocynkowanych koroduje o prawie 50% szybciej niż powłoka miedziana. Realna różnica miedzy dwoma typami uziomów jest jeszcze większa, ponieważ średnia grubość powłoki miedzianej wynosiła około 175 µm, czyli ponad dwa razy więcej niż w przypadku uziomów ocynkowanych (średnio 76 µm powłoki cynkowej na uziomie ze względu na tendencję powstawania pęknięć w powłoce cynkowej na uziomach stalowych z grubszą powłoką cynkową). Tak więc, jeśli porównać procentową utratę wagi uziomu w ciągu 28 dni testów z orginalną grubością powłoki ochronnej to okazuje się, że szybkość korozji uziomów ocynkowanych jest 3,38 razy większa niż dla ich odpowiedników pomiedziowanych. Innymi słowy, system uziemiający zbudowany na uziomach ocynkowanych ma okres eksploatacji z reguły krótszy niż 1/3 okresu eksploatacji systemu uziemiającego zbudowanego w oparciu o uziomy pomiedziowane.
Porównanie grup uziomów
Możliwa jest również głębsza analiza danych poprzez porównanie skrośne grup uziomów w zależności od grubości powłoki ochronnej, średnicy uziomu oraz typu uszkodzenia uziomów (zarysowanie lub wgniecenie). Tabela 2 przedstawia zróżnicowanie wyników przy podziale uziomów na ww. grupy.
Po zestawieniu wyników z różnych grup uziomów okazało się, że wzorce poddane celowemu uszkodzeniu nie różniły się swoimi właściwościami odporności na korozję od ich odpowiedników nienoszących takich uszkodzeń. Po drugie okazało się, że średnia utrata wagi jest stała dla wszystkich typów uziomów pomiedziowanych, bez względu na grubość powłoki miedzianej lub średnicę uziomu. Ta sama prawidłowość dotyczy uziomów stalowych ocynkowanych tylko odnośnie grubości powłoki ochronnej. W zależności od średnicy uziomy ocynkowane wykazują znaczne różnice w utracie wagi. W przypadku uziomów ocynkowanych 5/8” utrata wagi była znacznie większa, co wynika zapewne z większej powierzchni styku uziomu 5/8” z roztworem korozyjnym. Logiczną wydawałaby się prosta korelacja zmiany średnicy wzorców uziomów z utratą wagi uziomu. Pomimo, że pewne różnice procentowe tyczące się konkretnych uziomów były zauważalne, to ogólna tendencja pokazywała dobrą korelację ze średnią utratą wagi. Średnia wartość zmniejszenia średnicy uziomów dla uziomów pomiedziowanych i ocynkowanych, przy niedokładności w zakresie +/-2,54 µm, wynosiła odpowiednio 10,92 i 17,02 µm. Innymi słowy średnia utrata wagi była o około 50% większa w przypadku uziomów ocynkowanych.
Wnioski
Artykuł przedstawia metodę eksperymentalną oraz wyniki testu porównawczego odporności korozyjnej uziomów pomiedziowanych i ocynkowanych. Cała procedura oparta była na założeniu jak najbardziej realistycznego odtworzenia korozyjności wielu typów uziomów w oparciu o kontrolowany laboratoryjnie test korozyjności zgodnie z EN50164-2.
Podstawowe konkluzje wynikające z przeprowadzanych badań są następujące:
• uziomy stalowe ocynkowane korodują zdecydowanie szybciej niż ich odpowiedniki z pokryciem miedzianym,
• powłoka cynkowa na uziomach stalowych koroduje około trzy razy szybciej niż powłoka miedziana na uziomach pomiedziowanych,
• system uziemiający zbudowany w oparciu o uziomy ocynkowane będzie posiadał trwałość około 1/3 trwałości systemu uziemiającego opartego na uziomach pomiedziowanych,
• uwzględniając granicę błędu oraz zależności statystyczne wyniki wykazały, że typowe uszkodzenia uziomów, jak zarysowania i wgniecenia, nie mają wpływu na odporność korozyjną uziomów.
Wojciech Zdunek
Autor jest specjalistą
d/s techniczno-handlowych
Erico Eritech
Bibliografia
[1] Jeffrey R. „Corrosion rates of buried galvanised wires”, Corrosion & Prevention 98 Proceedings (1998): 316-320,
[2] Rabeler R. C. „Soil Corrosion Evaluation of Screw Anchors”, Effects of Soil Characteristics on Corrosion (1989): 54-80,
[3] Camitz G., Vinka T. G. „Corrosion of Steel and Metal – Coated Steel In Swedish Soils –Results of Field Exposures”, Proceedings of 10th Scandinavian Corrosion Congress NKM10 (1986): 305-312.