Falownik SieiDrive AVY 800 kW – rozruch silnika dużej mocy
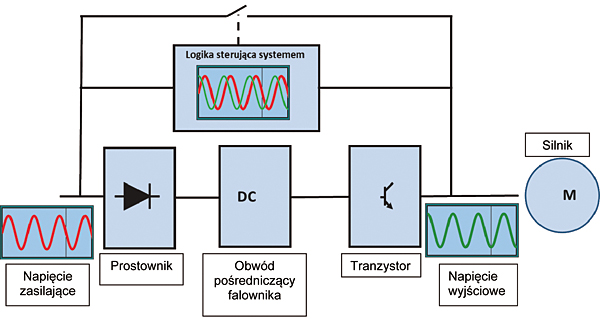
W artykule opisano realizację aplikacji do rozruchu silnika dużej mocy za pomocą falownika włoskiej firmy Gefran SieiDrive AVY 800 kW 3 x 400 V. Układ charakteryzuje się możliwością synchronizacji napięcia wyjściowego z siecią zasilającą. Wykorzystany został w instalacji skrawarki kalibratora drewna w zakładzie Kronopol w Żarach.
Rozruch silników dużej mocy stanowi dla przemysłu poważny problem, szczególnie gdy rozruch ten dotyczy silnika asynchronicznego. Podstawowym sposobem rozruchu jest tzw. rozruch bezpośredni, czyli podanie znamionowego napięcia zasilania. W takiej sytuacji silnik dąży do osiągnięcia znamionowej prędkości obrotowej w czasie 0 s. Skutkiem tego jest duży prąd rozruchu (często przekraczający pięcio- a nawet ośmiokrotnie prąd znamionowy) oraz bardzo duży udar mechaniczny, który może być przyczyną uszkodzenia samego silnika, jak i maszyny przez niego napędzanej. Wreszcie z konstrukcji silnika wynika, że w chwili załączenia stanowi on dla sieci zwarcie, co w pierwszym momencie dodatkowo ją obciąża.

Wykres prądu rozruchowego silnika podczas rozruchu bezpośredniego
Tego typu rozruchy stosuje się standardowo w silnikach rzędu kilku kW. Jeśli jednak chodzi o silnik 800 kW, udary mechaniczne przy rozruchu i koszt ich usuwania stanowią realne i poważne zagrożenie. Przewymiarowanie kabli, zabezpieczeń transformatorów i linii zasilających w taki sposób, aby rozruch bezpośredni był możliwy, staje się inwestycją bardzo drogą.
Wykorzystanie soft-startu
W takim przypadku jedną z popularnych i stosunkowo niedrogich metod rozruchu jest wykorzystanie soft-startu. Urządzenie to umożliwia zasilenie silnika obniżonym napięciem, które jest w kontrolowany sposób podnoszone i pozwala stopniowo doprowadzić parametry do wartości znamionowych. W ostatniej fazie rozruchu silnik jest już zasilany pełnym napięciem. Metoda ta eliminuje udary mechaniczne i pozwala, w pewnym stopniu, obniżyć prąd rozruchowy. Niestety rozruch taki zawsze jest kompromisem między wydajnością prądową instalacji i dopuszczalnym obciążeniem silnika, gdyż z kwadratem obniżanego napięcia obniża się moment napędowy silnika.

Wykres prądu rozruchowego silnika po zastosowaniu soft-startu
Falownik zamiast soft-startu
Bardzo dobre warunki rozruchu można uzyskać przy użyciu falownika. Umożliwia on bardzo łagodny rozruch, z dużym momentem rozruchowym i bez żadnych udarów dla sieci. Pozwala również na płynną regulację obrotów silnika. Jednak przypadek w zakładzie Kronopol pokazał, że są sytuacje, w których falownik również nie jest rozwiązaniem optymalnym.
W aplikacji skrawarki regulacja obrotów nie była potrzebna, a wręcz wskazane było, aby silnik pracował z prędkością znamionową. W takiej sytuacji falownik wprowadzał dodatkowe straty, co przy mocy 800 kW jest już wartością nie do pominięcia. Dodatkowym problemem był reżim pracy silnika. Wymagał on bardzo dużych przeciążeń, większych niż mógł zapewnić standardowy falownik. Oczywiście wykonanie falownika o odpowiednio większej przeciążalności nie stanowi problemu technicznego, jednak dla klienta oznaczało to cenę przekreślającą sensowność inwestycji.

Wykres prądu rozruchowego silnika po zastosowaniu falownika, bez synchronizacji

Wykres prądu rozruchowego silnika po zastosowaniu falownika z synchronizacją
W tej sytuacji pojawił się pomysł połączenia zalet soft-startu i falownika, czyli zbudowania falownika, który rozpędzi silnik do prędkości znamionowej, a po zakończeniu rozruchu przełączy go bezpośrednio na zasilanie sieciowe, podobnie jak robią to soft-starty.
Dzięki takiemu rozwiązaniu zyskuje się wszystkie zalety rozruchu z falownikiem, a jednocześnie eliminuje straty wynikające z ciągłej pracy tranzystorów falownika, i zachowuje przeciążalność ograniczoną tylko parametrami silnika i wydajnością sieci zasilającej.
Projekt aplikacji
Zagadnienie wydaje się z pozoru proste – należy rozpędzić silnik do prędkości znamionowej, odłączyć jedno źródło zasilania (falownik) i dołączyć główne źródło zasilania: sieć energetyczną. Silnik jest już rozpędzony, nie ma problemu z wytworzeniem momentu rozruchowego. Zatem po przełączeniu prąd płynący do silnika powinien mieć identyczną wartość, jak przed przełączeniem lub minimalnie większą – jeśli uwzględni się spadek prędkości obrotowej w czasie przełączenia i konieczność wytworzenia dodatkowego momentu, aby powrócić do prędkości znamionowej. W rzeczywistości, po odłączeniu zasilania, w silniku jeszcze przez pewien czas utrzymuje się strumień magnetyczny, który powoduje, że przez chwilę silnik działa jak prądnica – na jego zaciskach utrzymuje się napięcie. Jeżeli w chwili załączenia drugiej linii zasilającej, napięcia na zaciskach silnika i sieci będą z sobą zsynchronizowane – wszystko przebiegnie gładko. W przeciwnym razie do silnika popłynie prąd większy niż przy rozruchu bezpośrednim. Napięcie generowane przez standardowe falowniki w żaden sposób nie jest synchronizowane z siecią. Nie wiadomo zatem, czy w momencie przełączenia napięcia sieci i silnika będą z sobą zsynchronizowane.
Dodatkowym utrudnieniem jest kształt napięcia generowanego przez falownik, które zbudowane jest z szeregu prostokątnych impulsów wysokiej częstotliwości. Wiele układów pomiarowych nie potrafi poradzić sobie z poprawnym pomiarem takiego napięcia, a tym bardziej zsynchronizować go z sinusoidalnym napięciem sieci.
Inżynierowie Centrum Elektroniki Stosowanej CES znaleźli na to sposób. Po zsynchronizowaniu napięcia falownika i sieci wystarczyło tylko szybko przełączyć silnik na sieć. Pierwsza wersja urządzenia zbudowana została praktycznie bez elementów „myślących”. Jej zasadnicza część, odpowiadająca za synchronizację z siecią i wybranie właściwego momentu załączenia, została opracowana na bazie podzespołów wyprodukowanych w Polsce. Dla potrzeb tego projektu wewnątrz firmy CES wydzielono zespół inżynierów, którego zadaniem było opracowanie optymalnego rozwiązania. W ramach testów zbudowano stanowisko prób, będące modelem docelowej instalacji, zawierającej falownik, silnik, układ synchronizacji i układ przełączający. Model ten bardzo dobrze odzwierciedlał rzeczywiste warunki pracy aplikacji i umożliwił perfekcyjne przygotowanie automatyki.
Bardzo cenna okazała się także współpraca klienta, który przed uruchomieniem docelowego systemu umożliwił podłączenie falownika w próbnym układzie z zapasowym silnikiem i przetestowanie dostarczonych urządzeń bez zakłócania pracy linii technologicznej. Było to bardzo ważne z uwagi na krótki czas przestoju, podczas którego istniała możliwość podłączenia nowo dostarczonego falownika.
Kolejne dwa urządzenia, które pracują w zakładzie, zostały zbudowane z użyciem sterowników PLC. Umożliwiły one łatwe podłączenie do systemu AKPiA zakładu, a poprzez panele operatorskie usprawniły obsługę. Ta część systemu, która odpowiadała za synchronizację, okazała się na tyle niezawodna, że wykorzystano ją przy montowaniu kolejnych urządzeń.

Schemat blokowy podłączenia falownika do silnika
Falownik SieiDrive AVY
W opisanej aplikacji został zastosowany falownik w wersji szafowej SieiDrive AVY o mocy 800 kW firmy Gefran (zastąpiony teraz modelem ADV 200) w układzie zasilania trójfazowego 400 V. Bazując na kilkudziesięcioletnim doświadczeniu producent zaprojektował go i wykonał tak, aby spełniać wymagania dotyczące najwyższych standardów EMC i zapewnić niezawodną pracę, bez zakłócania działania innych urządzeń. W pojedynczej szafie znajduje się kompletny układ przemiennika częstotliwości (układ prostowniczy 6-pulsowy + moduł falownika), a także wyposażenie opcjonalne: wyłącznik główny, stycznik, elementy sterowania, filtry i dławiki wyjściowe / wejściowe.
Konstrukcja szafy zapewnia prostą instalację, łatwy dostęp do sekcji silnoprądowej oraz sterującej, ułatwiając tym samym montaż kabli siłowych i sterujących.
W układzie zastosowano chłodzenie wentylatorowe wysokiej wydajności, zapewniające przepływ powietrza 6900 m3/h. Prawidłowe odprowadzanie ciepła z szafy gwarantuje długi czas życia oraz bezusterkową pracę w wymagającym środowisku.
Z uwagi na dorywczy charakter pracy obwodów mocy falownika, kilka minut po zakończeniu rozruchu, gdy obwody mocy falownika nie wydzielają już ciepła, wentylatory zostają wyłączone. Poprawia to sprawność układu, wydłuża żywotność wentylatorów i znacząco zmniejsza ilość kurzu trafiającego do falownika, ograniczając częstotliwość i zakres prac konserwacyjnych przy urządzeniu.
mgr inż. Tadeusz Kantor
Autor jest Kierownikiem Działu Serwisu Energoelektroniki
w firmie Centrum Elektroniki Stosowanej
mgr inż. Rafał Witkowski
Autor jest specjalistą ds. napędów
w firmie Centrum Elektroniki Stosowanej