Przetwornice Danfoss VLT AutomationDrive FC 302 w instalacji spożywczej
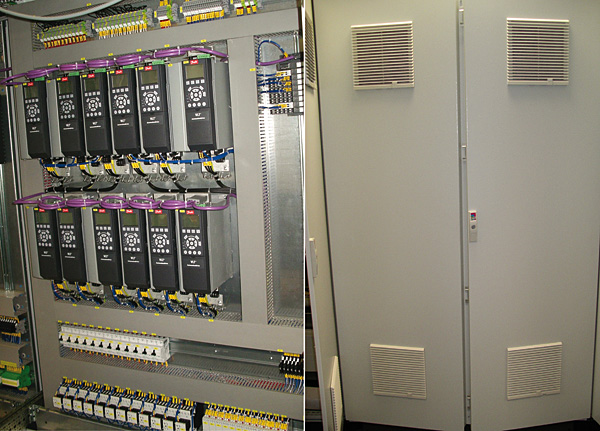
W artykule zostały zaprezentowane układy wielonapędowe z przetwornicami Danfoss serii VLT AutomationDrive FC 302, pracujące w instalacji produkcji mleka w proszku i nadzorowane magistralą Profibus. Autorem aplikacji jest firma Schulz Infoprod, która jako Autoryzowany Dystrybutor współpracuje z Danfoss od ponad 5 lat.
Stosowanie układów napędowych o regulowanej wydajności w automatyce przemysłowej staje się dziś standardem. Podyktowane jest to względami zarówno ekonomicznymi (optymalizacja zużycia energii) jak i możliwościami, jakie oferują obecne przetwornice częstotliwości. Popularność komunikacyjnych sieci polowych w rozwiązaniach sterowania procesów przemysłowych powoduje również, iż projektanci większych systemów coraz częściej stosują urządzenia wykonawcze jak przetwornice częstotliwości, siłowniki zaworów, przetworniki pomiarowe wyposażone w moduł komunikacyjny. Upraszcza to znacząco okablowanie obiektowe, zmniejsza liczbę wejść/wyjść analogowych i cyfrowych w sterowniku oraz daje łatwość obsługi z poziomu interfejsu operatora HMI. Ułatwia także diagnostykę usterek i prowadzenie działań serwisowych.

Rys. 1. Linia produkcji mleka w proszku wyposażona w układy wielonapędowe z przetwornicami Danfoss serii VLT AutomationDrive FC 302 nadzorowane magistralą Profibus
Koncepcja aplikacji
Wśród różnorodnych aplikacji falowników realizowanych przez firmę Schulz Infoprod, ciekawym zastosowaniem jest system sterowania procesem wytwarzania mleka w proszku. Złożoność technologii procesu wymagała w tym przypadku zastosowania szybkiego i wydajnego sterownika, przyjaznego systemu HMI, jak również efektywnych, regulowanych układów napędowych. System oparty jest o sterownik Siemens S7-400, rozproszoną sieć modułów I/O firmy Siemens, system SCADA Wonderware Platform oraz 54 sztuki falowników Danfoss serii VLT AutomationDrive FC302 z modułami komunikacyjnymi Profibus – rozmieszczone w kilku polach szafy sterowniczej, szafach lokalnych oraz jako samodzielne jednostki napędów o mocach powyżej 45 kW.
Jednym z głównych założeń przy projektowaniu systemu sterowania było uzyskanie dużej elastyczności sterowania napędami i minimalizacja połączeń kablowych. W związku z tymi wymaganiami zapadła decyzja o realizacji sterowania falownikami poprzez magistralę Profibus, a pozostałymi elementami obiektowymi poprzez magistralę ASi. Falowniki (o mocach mniejszych niż 45 kW) zostały zamontowane w zespole szaf sterowania napędów (MCC), falowniki o mocy większej niż 45 kW umieszczono poza szafami MCC – na obiekcie, w pobliżu urządzeń technologicznych.
Komunikacja Profibus
Falowniki Danfoss FC 302 dzięki swojej modułowości i wielu dostępnym opcjom dają duże możliwości sterowania, a większość funkcji falownika dostępna jest poprzez magistralę Profibus. W omawianym rozwiązaniu zastosowano w falownikach moduł Profibus DP V0/V1 typu MCA101 oraz moduł MCB107 – zasilania 24 V DC back-up.

Rys. 2. Przykładowy ekran programu MCT-10 – konfiguracja 27 falowników FC302
Moduł MCB107
Moduł MCB107 zainstalowany w falowniku daje możliwość komunikacji z falownikiem po odłączeniu jego zasilania sieciowego. Tak więc w sytuacji, gdy nastąpi odłącznie falownika – np. wyłączenie napędu wyłącznikiem remontowym lub zadziała zabezpieczenie sieciowe falownika – operator nadal dysponuje komunikacją z falownikiem i możliwością zdalnego zdiagnozowania przyczyny wyłączenia, a także wykonania restartu urządzenia po przywróceniu zasilania.
Moduł MCA101
Moduł MCA101 obsługuje dwa profile słowa sterującego Profibus:
• profil Profidrive, który jest przyjętą przez organizację Profibus specjalną wersją protokołu komunikacji Profibus dla układów napędowych z przemiennikami,
• profil Danfoss FC, który został opracowany specjalnie dla falowników Danfoss.
Szczegółowy opis programowania transmisji sterownik PLC – falownik, tj. wybór rodzaju danych/parametrów wymienianych pomiędzy PLC a falownikiem (wybór typu PPO), tworzenie ramki zapytania (CTW) i odczyt ramki odpowiedzi (STW) z falownika jest zawarty w instrukcji modułu MCA101. Instrukcja zawiera też przykłady fragmentów programów napisanych w języku Step 7 dla sterowników Siemens. Programista w łatwy sposób może przesłać wartość zadaną obrotów, poszczególne komendy do falownika i odczytać aktualny jego status.

Rys. 3. Ekran rejestracji Scope Folder w trybie PC Polling z wybranymi sześcioma parametrami falownika
Opisany sposób komunikacji z falownikami dotyczy całej rodziny falowników: FC 100, FC 200 i FC 300. Falowniki serii FC 100 stosowane są do aplikacji wentylacyjnych HVAC, serii FC 200 stosowane do aplikacji pompowych, serii FC 300 – do aplikacji stałomomentowych i aplikacji specjalnych. Dla każdego typu falownika producent udostępnia na swoich stronach internetowych pliki GSD, potrzebne do konfiguracji sprzętowej sieci Profibus.
Układy napędowe z falownikami obsługują różne urządzenia technologiczne, często o specyficznych wymogach, co do parametrów regulacji. Istnieje nieraz potrzeba, aby wybrane parametry falownika były zmieniane zależnie od wymogów danej fazy procesu. Oprócz możliwości zmiany nastaw, użytkownik powinien mieć możliwość zmiany parametrów falownika poprzez magistralę Profibus.
Profil Profidrive daje możliwość zmiany parametrów falownika w dwóch specjalnych trybach: DPV0 oraz DPV1 Master klasy 1 (np. sterownik PLC) i Master klasy 2 (np. komputer PC). Generalnie, bez wnikania w szczegóły programowania, oba tryby pozwalają na dostęp do parametrów falownika i ich zmianę. Tryb DPV1 daje większe możliwości, zwłaszcza możliwość komunikacji zarówno cyklicznej jak i acyklicznej, co pozwala na ciągły dostęp i zmianę większości parametrów falownika zarówno z poziomu urządzenia Master klasy 1 i Master klasy 2.
Architektura
W opisywanym systemie sterowania proszkownią mleka, główna szafa napędowa MCC zawiera 27 falowników FC 302 o łącznej mocy 272 kW, druga szafa napędowa – 27 falowników o łącznej mocy 946 kW. W szafach napędów umieszczono także moduły wejść/wyjść ET200S, przekaźniki interfejsowe oraz niezbędny osprzęt elektryczny.
Jednym z ograniczeń sieci Profibus jest maksymalny rozmiar segmentu sieci obejmujący maksymalnie do 31 jednostek typu slave. Jeśli struktura zawiera więcej niż 31 jednostek, dla kolejnego segmentu wymagany jest wzmacniacz (repeater). Jedna sieć Profibus z jednym urządzeniem Master może objąć maksymalnie 121 falowników plus 3 repeatery.
W zależności od prędkości transmisji (187,5 kBaud do 12 MBaud), maksymalna łączna długość jednego segmentu sieci Profibus z 31 falownikami może wynieść odpowiednio – 1000 m (przy 187,5 KBaud) i 100 m (przy 12 Mbaud). W opisanym systemie z 54 falownikami utworzono więc dwa segmenty sieci Profibus.

Rys. 4. Widok jednego z pól rozdzielnicy napędów oraz elewacji szafy
Program konfiguracyjny MCT-10
Przydatnym narzędziem, również wykorzystanym w omawianej aplikacji, jest oferowany przez firmę Danfoss program MCT-10. Ułatwia on i znacznie przyspiesza konfigurację i parametryzację za pomocą notebooka falowników połączonych magistralą Profibus, szczególnie przy ich większej ilości. W najprostszej konfiguracji program MCT-10 może komunikować się z pojedynczym falownikiem przez port USB. Kolejna konfiguracja to komunikacja z siecią falowników połączonych interfejsem RS 485. Jeśli konieczne jest połączenie się z siecią falowników spiętych magistralą Profibus – należy zastosować kartę Profibus (np. CP5511 firmy Siemens) zainstalowaną w notebooku.
Program umożliwia przygotowanie parametrów wszystkich falowników i, jeśli mają one wpisane wcześniej adresy Profibus, parametryzację wszystkich falowników przez sieć. Jest wygodnym narzędziem do uruchamiania i monitorowania pracy poszczególnych napędów. Oprócz szybkiej parametryzacji (parametry wybranego falownika można zmieniać on-line) pozwala na przeglądanie aktualnych alarmów, ostrzeżeń i rejestru błędów wybranego falownika – maksymalnie do 200 alarmów i ostrzeżeń. Są one aktualizowane w każdym cyklu zapisu/odczytu danych z falownika.
Funkcja Scope Folder
Program MCT-10 umożliwia także monitorowanie bieżących parametrów wybranego napędu. Służy do tego funkcja Scope Folder, w której można zdefiniować maksymalnie sześć kanałów rejestracji parametrów (np. prąd napędu, napięcie DC, wartość zadaną Profibus itp.). Dostępne są dwa tryby rejestracji parametrów: tryb PC Polling Chanel oraz tryb Drive Real Time Channel. W pierwszym można rejestrować parametry od umownego czasu 0:00:00 startu rejestracji, w drugim można rejestrować od momentu wybranego zdarzenia. Jeśli istnieje potrzeba zapisywania parametrów w przypadku wystąpienia konkretnego zdarzenia – np. przekroczenia ograniczenia prądowego – stosuje się tryb Drive Real Time Channel, w którym można zdefiniować sposób wyzwalania rejestracji przy wystąpieniu tego zdarzenia. Program Scope Folder umożliwia także eksport zapisanych danych do pliku Excel w celu dalszej ich obróbki.
Moduł SLC
Wszystkie falowniki Danfoss rodziny FC mają wbudowany moduł programowy SLC (sekwencyjny sterownik zdarzeń). Prosty edytor typu graf przejść (będący modułem programu MCT-10) pozwala na zdefiniowanie zachowania się falownika przy wystąpieniu określonego warunku logicznego, wyniku operacji porównania, osiągnięcia stanu licznika itp. Dowolne zdarzenie zdefiniowane w module SLC może generować opisany wcześniej start rejestracji wybranych parametrów falownika w archiwum Scope Folder.
Inne elementy aplikacji
W trakcie projektowania szaf napędowych MCC ważnym aspektem był ich system chłodzenia. Pomieszczenie rozdzielni, w którym umieszczone są szafy, jest klimatyzowane i zapewnia odpowiednie parametry powietrza chłodzącego. Dla zapewnienia cyrkulacji powietrza chłodzącego w szafie, każde z pól szafy wyposażono w wentylatory nawiewne oraz kratki wywiewne (rys. 4). Sumaryczny wymagany przepływ powietrza chłodzącego falowniki został zapewniony przez dobór wentylatorów o odpowiedniej wydajności.
Wszystkie jednostki FC302 wyposażono dodatkowo w lokalne panele LCP, co jednak nie było konieczne, ze względu na pełną diagnostykę falowników prowadzoną magistralą Profibus z poziomu systemu sterowania. Wymagało to pewnych dodatkowych nakładów pracy ze strony programistów sterownika PLC – w tym przypadku Siemens S7-400.
Podczas uruchamiania systemu czas spędzony przez inżyniera rozruchu przy testowaniu i ustawianiu napędów okazał się znacznie krótszy niż w podobnej wielkości aplikacjach z tradycyjnym sterowaniem analogowo-cyfrowym. Rozruch przebiegał sprawnie, a wszystkie kolejne konfiguracje falowników zostały na bieżąco udokumentowane w odpowiednich plikach archiwum serwisowego.
Lech Ptaszyński
Autor jest projektantem automatyki firmy Schulz Infoprod