Przetworniki pomiarowe i czujniki w układach automatyki przemysłowej
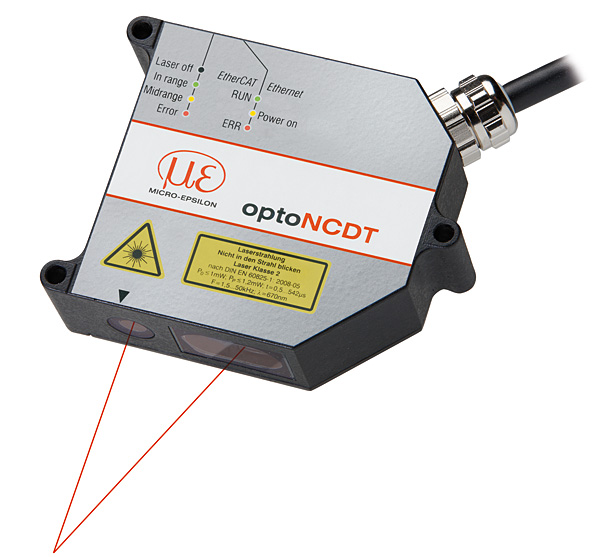
Przetworniki pomiarowe i czujniki dostarczają dane niezbędne do zarządzania procesami przemysłowymi
Do realizacji podstawowych zadań systemów automatyki niezbędne są pomiary parametrów procesów technologicznych i wykorzystanie uzyskanych sygnałów do regulacji i sterowania tymi procesami. Parametry te są z reguły wielkościami nieelektrycznymi, jak np. temperatura, ciśnienie, przepływ, poziom i najczęściej pomiary tych wielkości są realizowane metodami elektrycznymi. Do pomiarów służą przetworniki pomiarowe i czujniki, czyli elementy układu pomiarowego reagujące na zmiany określonych wielkości fizycznych.
Przetwornik pomiarowy jest urządzeniem służącym do przetwarzania – z określoną dokładnością i z uwzględnieniem odpowiednich praw fizycznych – sygnału pomiarowego, tzn. sygnału zawierającego informacje o wartościach mierzonych wielkości fizycznych i związkach zachodzących między nimi. Przetwornik pomiarowy może być samodzielnym urządzeniem pomiarowym lub może stanowić część układu pomiarowego (może współpracować z czujnikiem). Sygnał wejściowy i przetworzony sygnał wyjściowy przenoszą informacje w postaci liczb. W ogólnym modelu przetwornika pomiarowego rozróżnia się nośniki i treści sygnału. Nośnikami są wielkości fizyczne, np. napięcie elektryczne, temperatura, ciśnienie, zaś treściami są liczby odpowiadające wartościom tych wielkości, np. określona wartość napięcia czy temperatury.
W zależności od postaci sygnałów rozróżnia się przetworniki pomiarowe:
• analogowe (a/a) – przetwarzające sygnał wejściowy analogowy na sygnał wyjściowy również analogowy, np. przekładnik napięciowy, transformujący napięcie wysokie na niskie lub przetwornik pomiarowy ciśnienia na prąd elektryczny,
• analogowo cyfrowe (a/c) – przetwarzające sygnał wejściowy analogowy na sygnał wyjściowy cyfrowy, np. przetwornik analogowy prądu elektrycznego na sygnał cyfrowy w kodzie dwójkowym,
• cyfrowo analogowe (c/a) – o działaniu odwrotnym niż przetwornik analogowo cyfrowy,
• cyfrowo cyfrowe (c/c) – przetwarzające sygnał wejściowy cyfrowy na sygnał wyjściowy również cyfrowy, np. przetwornik pomiarowy sygnału w kodzie dwójkowym na sygnał w kodzie dziesiętnym.
Wśród przetworników pomiarowych analogowych występują przetworniki skali wielkości, które nie zmieniają natury fizycznej ani kształtu przebiegów czasowych nośnika sygnału. Dzieli się je na nieelektryczne (np. mechaniczne) i elektryczne (np. przetworniki pomiarowe napięcia na napięcie, prądu na prąd lub napięcia na prąd i prądu na napięcie). Większość używanych w praktyce urządzeń tego typu stanowią przetworniki pomiarowe elektryczne, tzn. takie, w których przynajmniej jeden z sygnałów – wejściowy lub wyjściowy – jest sygnałem elektrycznym.
Rozróżnia się też przetworniki pomiarowe skali wielkości pasywne i aktywne. Przetworniki pasywne całą energię zużywaną w procesie przetwarzania czerpią ze źródła sygnału wejściowego (np. dzielniki napięcia, przekładniki prądowe). Przetworniki aktywne czerpią energię ze źródła zewnętrznego (np. przetworniki pomiarowe ze wzmacniaczem operacyjnym i sprzężeniem zwrotnym).
Przetworniki pomiarowe można, podobnie jak czujniki, podzielić na generacyjne i parametryczne. Wyróżnia się też przetworniki pomiarowe standaryzujące tzn. takie, których sygnał wyjściowy jest znormalizowany. Standardowe sygnały wyjściowe mogą być prądowe lub napięciowe. Prądowe sygnały wyjściowe analogowe do współpracy z urządzeniami wtórnymi mogą mieć np. formę: 0 – 5 mA, 0/4 – 20 mA, ±5 mA. Napięciowe sygnały znormalizowane to np. 0 – 10 mV, 0 – 10 V, 4 – 20 V.
W aparaturze kontrolno-pomiarowej występują jeszcze wyjścia transmisyjne, częstotliwościowe, impulsowe, cyfrowe (interfejsy), m.in. RS232C, RS485, wyjścia napięciowe do sterowania blokiem tyrystorowym itd. Do najczęściej stosowanych standardowych sygnałów wyjściowych przetworników pomiarowych należą: sygnał prądowy 0/4 – 20 mA i napięciowy 0 – 10 V.

Termorezystorowy czujnik temperatury SA2 firmy Introl – w wykonaniu aseptycznym do przemysłu spożywczego i farmaceutycznego
Czujniki
W układach automatyki obok przetworników pomiarowych występują czujniki wielkości fizycznych reagujące na ich zmiany lub obecność. Mierzona przez czujnik wielkość przetwarzana jest na sygnał elektryczny, standardowy analogowy lub cyfrowy, nadający się do transmisji. Odbywa się to bezpośrednio w czujniku lub we współpracującym z nim przetworniku pomiarowym. Niektóre czujniki reagują bezpośrednio na mierzoną wielkość fizyczną, inne generują sygnał, który jest mierzony dopiero po zakłóceniu go przez obiekt, np. po odbiciu od obiektu przy pomiarach odległości. Czujniki tego rodzaju reagują zazwyczaj na wartości wielkości mierzonej, ale też na zakłócenia i zasilanie. W odpowiednio wykonanych czujnikach wpływ zasilania i zakłóceń na sygnał wyjściowy jest ograniczany.
Podstawowy układ pomiarowy do pomiarów wielkości nieelektrycznych składa się zazwyczaj z trzech elementów: czujnika, przetwornika i odbiornika (miernika, regulatora, sterownika). Czujnik przetwarza mierzoną wielkość nieelektryczną na sygnał elektryczny, dalej przetwornik przetwarza ten sygnał na sygnał znormalizowany, nadający się do transmisji. Przyrząd pomiarowy wskazuje analogowo lub cyfrowo wartość wielkości mierzonej przetworzonej na sygnał znormalizowany. Znormalizowanie sygnału wyjściowego umożliwia stosowanie tej samej aparatury, odpowiednio wyskalowanej, do pomiarów różnych wielkości fizycznych.
Wśród czujników wyróżnia się czujniki parametryczne – pasywne – i czujniki generacyjne – aktywne. Czujniki parametryczne to urządzenia, których wielkością wyjściową jest zmiana parametru elektrycznego, np. rezystancji, pojemności, indukcyjności pod wpływem czynnika mierzonego. W czujnikach generacyjnych wielkością wyjściową jest prąd lub napięcie przez nie wytworzone.
Czujnik pomiarowy nie powinien wpływać na wielkość mierzoną, np. nie może on ogrzewać miejsca pomiaru. Warunek ten mogą spełniać tylko czujniki o niewielkiej mocy sygnału wyjściowego. Potrzebny jest wówczas dostatecznie czuły układ pomiarowy, np. mostkowy lub z elektronicznym wzmacnianiem sygnału pomiarowego.
Czujniki temperatury
Do pomiarów temperatury stosowane są czujniki parametryczne – rezystancyjne oraz generacyjne – termopary (termoelementy). W termorezystorach parametrycznych wykorzystuje się wpływ wielkości mierzonej na rezystancję elementu pomiarowego. W czujnikach generacyjnych – termoparach wykorzystuje się powstawanie siły elektromotorycznej w termoogniwie pod wpływem różnicy temperatur między jego końcami.
Termorezystory
Dzięki temu, że metale charakteryzują się dodatnim współczynnikiem temperaturowym, możliwe jest konstruowanie termorezystorów do pomiaru temperatur zarówno dodatnich, jak i ujemnych. Stosowane są termorezystory platynowe, niklowe i niekiedy miedziane. Charakterystyki termorezystorów platynowych i miedzianych są liniowe, zaś niklowych wyraźnie nieliniowe. W technice pomiarów temperatury szczególne miejsce zajmują termorezystory platynowe. Umożliwiają one bowiem odtworzenie międzynarodowej praktycznej skali temperatur. Platynowe i niklowe czujniki rezystancyjne reagują na zmiany temperatury zmianą rezystancji wbudowanego w nie rezystora. Zazwyczaj termorezystor umieszczony jest w obudowie w formie rury zakończonej głowicą aluminiową. W głowicy umieszczony jest przetwornik przetwarzający zmiany rezystancji termorezystora na znormalizowany sygnał prądowy, np. 4 – 20 mA.
Czujniki generacyjne – termopary
Czujniki termoelektryczne (termopary) reagują na zmiany temperatury zmianami siły termoelektrycznej. W osłonie ochronnej umieszczony jest termoelement pojedynczy lub podwójny, niekiedy potrójny, oraz zaciski do przyłączenia elektrycznych przyrządów pomiarowych. Niekiedy w głowicy umieszcza się przetwornik siły termoelektrycznej na sygnał prądowy lub napięciowy.

Przetwornik CCA-200 firmy Simex do pomiaru ciśnienia mediów czystych, nieagresywnych, w warunkach przemysłowych

Przetwornik Vegabar 14 firmy Vega do ciągłego pomiaru ciśnienia
Czujniki ciśnienia
Do miejscowych pomiarów ciśnienia stosuje się zazwyczaj różnego typu manometry, których działanie oparte jest na rurce Bourdona. Służą one do pomiaru ciśnień wszystkich mediów gazowych i płynnych nieagresywnych i niekrystalizujących. Rozwinięciem konstrukcji prostych manometrów mechanicznych są manometry z wyjściem znormalizowanych sygnałów analogowych (4 – 20 mA), z wyświetlaczem LCD lub z mikrowyłącznikami. Mogą one służyć do regulacji procesów technologicznych. Często, ze względu na wady ustrojów mechanicznych, są one zastępowane czujnikami elektronicznymi.

Rodzina przepływomierzy elektromagnetycznych Proline Promag firmy Endress+Hauser
Pomiary przepływu
W procesach technologicznych obok pomiarów temperatury i ciśnienia kluczową pozycję zajmują pomiary przepływu i poziomu. Znanych jest wiele metod pomiarowych tych wielkości. Poniżej opisano niektóre z nich.

Ultradźwiękowy czujnik poziomu i odległości MIC+ 600 firmy Microsonic (fot. Introl)
Przepływomierze ultradźwiękowe
W zależności od wymagań procesowych i warunków obiektowych przepływ w rurociągach może być mierzony lub sygnalizowany. Sygnalizatory przepływu mają wyjścia dwustanowe. Zazwyczaj sygnalizują przekroczenia natężenia przepływu poniżej lub powyżej określonej wartości, mogą również służyć do jego regulacji. Do pomiaru natężenia przepływu stosowane są różnego rodzaju przepływomierze, które wartość zmierzoną przetwarzają na znormalizowany sygnał analogowy lub cyfrowy, proporcjonalny do przepływu. Do pomiarów przepływu stosowane są przepływomierze o różnych zasadach działania, np. elektromagnetyczne, owalnokołowe, różnicy ciśnień, wirnikowe, turbinowe, kalorymetryczne. Jedną z konstrukcji są przepływomierze ultradźwiękowe.
W rurociągach zamkniętych do pomiarów przepływu najczęściej stosuje się dwa rodzaje przepływomierzy ultradźwiękowych: wykorzystujących pomiar czasu przebiegu sygnału w przepływającym medium mierzonym oraz wykorzystujących zjawisko Dopplera.
Urządzenia z pierwszej grupy mierzą różnicę czasu przebiegu dwóch sygnałów dźwiękowych w przepływającym medium w odcinku rurociągu o określonej długości. Jeden sygnał jest wysyłany w kierunku zgodnym z kierunkiem przepływu medium, drugi zaś w kierunku przeciwnym. Prędkość przepływu mierzonego medium wynika z różnicy czasów przebiegu wysłanych sygnałów ultradźwiękowych. W przepływomierzach wykorzystujących zjawisko Dopplera najczęściej wysyłany jest ciągły sygnał dźwiękowy o stałej częstotliwości.
Przepływomierze ultradźwiękowe na ogół umożliwiają:
• pomiar przepływu objętościowego w standardowych jednostkach objętości,
• zliczanie objętości,
• pomiar przepływu masowego w standardowych jednostkach masy,
• zliczanie masy,
• pomiar prędkości fali dźwiękowej w ośrodku.
Pomiar jest niezależny od zmian temperatury cieczy, jej gęstości, ciśnienia i przewodności elektrycznej.
Przepływomierze elektromagnetyczne
Zasada działania przepływomierzy elektromagnetycznych polega na pomiarze siły elektromotorycznej indukowanej zgodnie z prawem Faradaya w cieczy przewodzącej przepływającej w zmiennym polu magnetycznym elektromagnesu zasilanego napięciem wolnozmiennym. Między elektrodami umieszczonymi na drodze przepływającej cieczy powstaje napięcie. Napięcie to jest próbkowane i przetwarzane na sygnał wyjściowy analogowy lub cyfrowy, proporcjonalny do prędkości przepływu cieczy. Przepływomierz nie zawiera wewnętrznych części mechanicznych, co pozwala na niezakłócony przepływ mierzonego medium pełnym przekrojem rurociągu. Pomiar przepływu jest niezależny od ciśnienia cieczy, jej lepkości i gęstości, temperatury i przewodności elektrycznej (powyżej wartości minimalnej).
Przetwornik przepływomierza elektromagnetycznego zazwyczaj składa się ze wzmacniacza sygnału, układu eliminującego zakłócenia i dryft zera, układu detekcji przepływu wstecznego i przetwornika. Część cyfrowa przetwornika oddzielona jest galwanicznie od pozostałych obwodów. Zawiera ona specjalizowany mikroprocesor wyposażony w zegar czasu rzeczywistego RTC, nieulotną pamięć statyczną oraz układy programowalne.
Pomiary poziomu
W zakresie urządzeń do pomiaru poziomu oferowane są m. in.:
• sygnalizatory poziomu,
• regulatory poziomu,
• magnetostrykcyjne przetworniki poziomu,
• hydrostatyczne sondy głębokości do pomiarów poziomu cieczy w zbiornikach, studniach głębinowych, poziomu ścieków itp.,
• ultradźwiękowe mierniki do ciągłe
go bezkontaktowego pomiaru poziomu w zbiornikach otwartych i zamkniętych,
• pojemnościowe czujniki poziomu do ciągłego pomiaru poziomu cieczy oraz materiałów sypkich w studniach, zbiornikach, zasobnikach silosach itp.
Pływakowe regulatory poziomu
Pływakowe dwustanowe sygnalizatory poziomu mogą być stosowane do regulacji poziomu cieczy, np. wody, kwasów, zasad, olejów ścieków, szlamów, sygnalizacji alarmowej maksimum/minimum i do bezpośredniego sterowania pompą w zbiornikach zamkniętych, otwartych i ciśnieniowych. W zależności od wykonania mogą pracować w cieczach agresywnych.
Ultradźwiękowe mierniki poziomu
Ultradźwiękowe mierniki poziomu i objętości (sondy ultradźwiękowe) działają na zasadzie pomiaru czasu między wysłaniem impulsu pomiarowego i odebraniem echa. Czas ten jest przetwarzany przez przetwornik elektroniczny sondy na sygnał wyjściowy. Mogą one mierzyć poziom i objętość większości cieczy i pulp (mas gęstopłynnych) w zbiornikach otwartych i zamkniętych, w zbiornikach magazynowych i w prostych zbiornikach procesowych. Są głównie przeznaczone do stosowania w przemyśle chemicznym i w gospodarce wodno-ściekowej.
Przetworniki ultradźwiękowe są wyposażane w zintegrowane wewnętrzne czujniki temperatury służące do kompensacji zmian temperatury otoczenia. Elektronika miernika przetwarzając odbite impulsy potrafi je zidentyfikować i oddzielić od fałszywego echa pochodzącego od mieszadeł, zakłóceń elektrycznych, akustycznych itp.
Sondę ultradźwiękową instaluje się nad powierzchnią mierzonej cieczy, prostopadle do jej powierzchni. Kondensacja pary wodnej na głowicy pomiarowej, spieniona lub falująca powierzchnia mierzonego medium negatywnie wpływają na wynik pomiaru, a nawet mogą go uniemożliwić.

OptoNCDT 2300 – laserowy czujnik triangulacyjny firmy Micro-Epsilon. Nadaje się do szybkich i precyzyjnych pomiarów względem powierzchni bezpośrednio odbijających światło (fot. Wobit)
Pojemnościowe czujniki poziomu
Do pomiarów wielkości fizycznych metodami pojemnościowymi wykorzystywane są zmiany pola elektrycznego między okładzinami kondensatora. Jedną elektrodę kondensatora stanowi izolowana lub nieizolowana sonda czujnika, drugą zaś metalowa ścianka zbiornika, a w przypadku zbiorników z tworzyw nieprzewodzących – sonda pomocnicza w postaci pręta umieszczonego w pobliżu sondy pomiarowej i do niej równoległego lub rury umieszczonej koncentrycznie wokół sondy pomiarowej. Dielektrykiem między okładzinami tak utworzonego kondensatora jest medium w zbiorniku, gaz ponad poziomem medium i ewentualnie izolacja sondy pomiarowej. Zmiana poziomu mierzonego medium powoduje zmianę pojemności kondensatora i wraz z nią zmianę jego impedancji, która przetwarzana jest na sygnał elektryczny. Do pomiaru poziomu cieczy przewodzących stosowane są sondy izolowane, zaś do pomiaru poziomu cieczy nieprzewodzących sondy nieizolowane. Czujniki pojemnościowe nie wymagają konserwacji, nie zużywają się, dają bardzo wyraźne impulsy bez iskrzenia i drgań zestyków.
Czujniki zbliżeniowe
Bezdotykowe czujniki zbliżeniowe z wyjściami półprzewodnikowymi lub przekaźnikowymi są powszechnie stosowane w automatyce przemysłowej. Ich zadaniem jest wykrywanie i sygnalizacja obecności różnego rodzaju obiektów: przedmiotów metalowych i niemetalowych, cieczy i gazów. Stosowane są m.in. jako wyłączniki krańcowe i bezpieczeństwa, a także wykorzystywane jako elementy wejściowe pozycjonerów, liczników przedmiotów, układów kontroli prędkości, systemów kontroli dostępu i alarmowych. Ich zalety to brak bezpośredniego kontaktu z wykrywanym obiektem, brak części ruchomych, duża szybkość działania, prostota stosowania, odporność na wpływy środowiskowe.
Czujniki zbliżeniowe można podzielić na dwie grupy: wytwarzające sygnał dwustanowy, np. odpowiadający zamknięciu i otwarciu obwodu oraz takie, które wytwarzają sygnał w przybliżeniu proporcjonalny do wielkości mierzonej. Spośród znanych konstrukcji czujników zbliżeniowych najpopularniejsze są czujniki indukcyjne i pojemnościowe.
Czujniki indukcyjne
Czujniki indukcyjne reagują na zbliżanie metalu do czoła czujnika. Ich najważniejszym parametrem jest strefa działania, czyli zakres czułości. Czujniki te reagują na wszystkie metale, ale intensywność działania zależy od rodzaju zbliżanego metalu. Znamionowa strefa działania wyznaczana jest dla stali. Przy innych metalach strefa ta jest krótsza i można ją wyznaczać za pomocą współczynników korekcyjnych podawanych przez producentów.
Działanie czujnika indukcyjnego polega na indukowaniu prądów wirowych w metalu wprowadzonym do pola czułości czujnika. Indukowane prądy wirowe wpływają na pole elektromagnetyczne wytwarzane wokół czoła czujnika przez obwód indukcyjny LC generatora wysokiej częstotliwości. Amplituda generowanego napięcia kontrolowana jest przez układ progowy. Amplituda ta maleje wraz ze zbliżaniem się metalu. Włączanie czujnika następuje po przekroczeniu częstotliwości progowej, wyłączanie zaś wówczas, gdy częstotliwość spadnie poniżej progu wyłączania. Zjawisko to nazywa się histerezą częstotliwości, wyrażaną w procentach i najczęściej zawierającą się w granicach 5 – 15%.
Czujniki pojemnościowe
Zasada działania czujników pojemnościowych polega na detekcji zmian pola elektrycznego przed ich czołem. Strefa czułości kształtowana jest przez dwie koncentrycznie umieszczone elektrody metalowe tworzące kondensator. Pomiędzy elektrodami (okładzinami kondensatora) powstaje pole elektryczne. Przedmiot wprowadzony w pole elektryczne kondensatora powoduje zmianę jego pojemności. Wraz ze zmianą pojemności układu zmienia się impedancja czujnika. Zmiana impedancji zamieniana jest w sygnał wyjściowy. Gdy w polu czułości czujnika znajdzie się wykrywany przedmiot (w odległości mniejszej od ustalonej wartości progowej), oscylator czujnika z dwoma płaskimi elektrodami wzbudza się przy pewnej pojemności układu i generuje drgania. Im mniejsza jest stała dielektryczna wykrywanego materiału, tym mniejsza musi być jego odległość od czoła czujnika niezbędna do przełączenia czujnika. Po oddaleniu czujnika od przedmiotu generowanie drgań zostaje przerwane. Czułość i histerezę czujnika można regulować przez zmianę parametrów generatora.
Czujniki pojemnościowe stosowane są przede wszystkim do wykrywania materiałów przewodzących lub nieprzewodzących prąd elektryczny w stanie stałym, sproszkowanym lub ciekłym, jak np. metale, szkło, ceramika, plastik, drewno, papier, karton olej, woda. Służą m.in. do pomiarów poziomu cieczy w zbiornikach szklanych i plastikowych, do sygnalizacji zerwania taśmy.
Opracowano na podstawie
materiałów firmowych
i stron www