Poprawa jakości uziemienia – rozwiązania fhu Partner
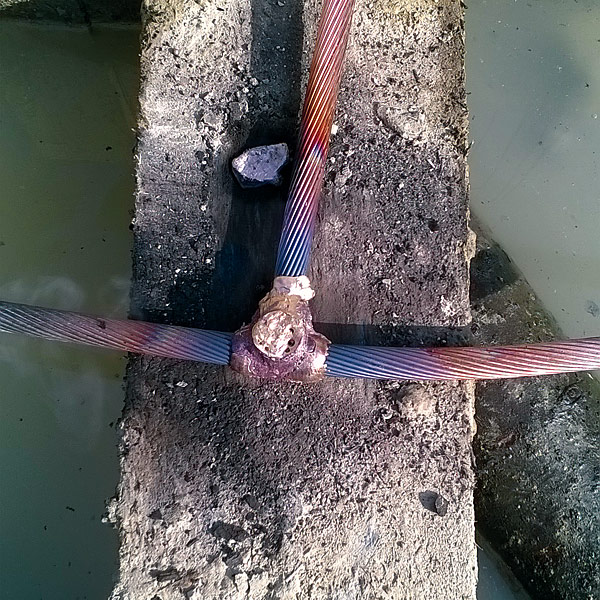
Warunki zastane w miejscu realizacji systemu uziemiającego niekiedy uniemożliwiają uzyskanie odpowiednio niskiej rezystancji uziemienia, nawet w przypadku jego prawidłowego zaprojektowania i wykonania. Artykuł prezentuje praktyczne metody poprawy jakości przewodzenia do ziemi z wykorzystaniem kilku dostępnych i sprawdzonych technologii.
Zarówno w przypadku wykonania pojedynczego uziemienia, budowy systemu uziemiającego – roboczego bądź dla urządzenia – celem jest uzyskanie określonej, niskiej rezystancji. Jej pożądana wielkość opisana jest w normach lub wynika z obliczeń. Rezystancja uziomu lub systemu uziemiającego musi być rozpatrywana w kontekście przyjętego projektowo czasu jego eksploatacji, a także warunków urbanistycznych, geologicznych i hydrologicznych, co z kolei determinuje dobór odpowiednich rozwiązań technologicznych i materiałów. Niekiedy jednak zastane warunki na działce obiektu znacznie utrudniają lub wręcz uniemożliwiają realizację założeń projektowych. Takie sytuacje zdarzają się na placach budów nowych obiektów i równie często w obiektach remontowanych.
Pomijając kwestie prawne, normatywne, doboru lokalizacji dodatkowych uziemień itp., często możliwe jest rozwiązanie takiej trudności w praktyczny sposób, bezpośrednio w miejscu instalacji. Zdarza się bowiem, że podejście do problemu od spodu (bottom-up) pozwala bardzo kreatywnie, w kluczowym momencie, znaleźć właściwe wyjście z sytuacji zastanej na budowie. Artykuł przybliża zalety i wady poszczególnych systemów uziemień pionowych, których użycie jest podstawową metodą redukcji rezystancji systemu uziemiającego, ale które mogą też pełnić rolę samodzielną; wskazuje na znaczenie połączeń pomiędzy elementami; opisuje właściwości uziomów mineralnych – jako metody trwałej poprawy wyników uziemienia.
Zastosowanie uziomów pionowych
W przypadku braku zakładanych parametrów siatki uziemiającej, najczęściej stosowanym, prawidłowym rozwiązaniem jest dozbrojenie uziomu otokowego (wykonanego z bednarek, linek czy drutu) uziomami pionowymi. Uziomy te stają się wówczas integralną częścią całego systemu. Dobór właściwych prętów powinien być podporządkowany trzem czynnikom. Po pierwsze warunkom geologicznym działki, czyli realnym możliwościom pogrążania prętów, po drugie przewidywanej żywotności całego systemu, tak aby trwałość poszczególnych elementów była zbieżna, po trzecie projektowanemu obciążeniu całego systemu, co w sposób znaczący może wpłynąć na trwałość połączeń między elementami systemu, jako że te zazwyczaj są najsłabszymi ogniwami. W pracy całego systemu ważną zaletą uziemień pionowych jest znacznie pewniejsza (stabilniejsza) rezystancja w długim okresie (zakładając wykonanie ich z trwałych materiałów).
Wspomnianym już, drugim przeznaczeniem uziomów pionowych jest ich samodzielna praca, zwłaszcza w dwóch przypadkach – fundament jest już wylany (co jest równoznaczne z niemożliwością zastosowania uziomu fundamentowego) i brak przygotowanego wykopu pod otok. Wówczas, zestawiając cenę poprawnego przygotowania wykopu i układania w nim bednarki (czy innego przewodnika) z punktowymi uziemieniami pionowymi, rachunek ekonomiczny przemawia zdecydowanie na korzyść tych drugich.
Punktowe uziemienia pionowe sprawdzą się również lepiej, jeżeli teren montażu jest z różnych względów trudny – remont jest realizowany w terenie utwardzonym, miejskim, zanieczyszczonym gruzem itd. Wbicie uziomów o dużej średnicy (3/4”), o solidnej miedzianej powłoce (minimum 254 mm), wykonanych z atestowanej stali, łączonych wytrzymałymi złączkami z brązu i wyposażonych w solidny grot pozwala szybko i efektywnie kosztowo uzyskać zakładaną rezystancję nawet w trudnych gruntach. Dodatkowo, w przypadku uziemienia pionowego znacznie łatwiej zapanować nad ostateczną rezystancją, niż w przypadku uziemień otokowych. Można to uzyskać, pogrążając kolejne uziemienia aż do uzyskania wyniku pożądanego – bez wykonywania wykopów, rozbierania bruku, kucia asfaltu, zajmowania chodnika itp. Uziemienia pionowe są bardzo przydatne, gdy zabezpieczany budynek już stoi, a zwłaszcza gdy brak jest miejsca i warunków na wykopy.
Dobór uziomów pionowych
Istotnym zagadnieniem jest dobór właściwych prętów spośród szerokiego wachlarza produktów dostępnych w ofertach hurtowni i dystrybutorów. Jeśli celem inwestora jest znalezienie rozwiązania trwałego w dłuższym okresie, wybór powinien paść na uziemienia pomiedziowane o minimalnej powłoce miedzi 250 mm. W uziomach tych można wyróżnić dwa podstawowe systemy łączenia prętów – złączkowy i bezzłączkowy.

Rys. 1. Połączenie uziomów pomiedziowanych gwintowanych firmy Erico
Łączenie bezzłączkowe i złączkowe
Na polskim rynku zdecydowanie przeważają uziemienia bezzłączkowe, gdzie każdy uziom wyposażony jest w bolec i wpust. Pomijając kwestię jakości powłok miedzianych, które często pozostawiają wiele do życzenia, a niekiedy nie spełniają norm, uziemienia łączone wtykowe cechują się szeregiem wad wynikających bezpośrednio z ich konstrukcji. Są to przede wszystkim:
• łatwość wyboczenia przy pogrążaniu, co jest wynikiem braku właściwej sztywności na połączeniach kolejnych uziomów,
• ryzyko rozłączenia przy źle zaprojektowanym systemie bolec-wpust lub dużym wyboczeniu spowodowanym głębokością pogrążania,
• zdzieranie się powłoki miedzi z powodu braku efektu tunelowania, wywoływanego przez grot i kontynuowanego przez złączki (w powszechnej opinii efekt tunelowania jest niekorzystny, gdyż skutkuje gorszym przyleganiem uziomu do gruntu a przez to większą rezystywnością. W praktyce jednak tunelowanie skutecznie zwiększa szansę na pogrążenie uziomów bez naruszenia powłoki miedzi, odsuwając od uziomu większe frakcje (kamienie, gruz). Natomiast w wyniku drgań pogrążanego uziomu główna część ziemi osypuje tunel przywracając prawidłowe przyleganie uziomu. W efekcie rezystancja mierzona zaraz po pogrążaniu jest o około 10-15% wyższa od mierzonej w uziemieniu łączonym bolec-wpust, a poziomy wyrównują się w ciągu 3-7 dni. Należy dodać, że uziomy skręcane mogą być pogrążane znacznie głębiej, gdzie z reguły rezystywność gruntu jest zdecydowanie lepsza),
• trudności w głębokim pogrążaniu,
• niska trwałość połączenia miedzy uziomami, ponieważ bolec pokryty miedzią wchodzi we wpust niezabezpieczony korozyjnie, dodatkowo powiększając go minimalnie w wyniku sił działających przy pogrążaniu. Całość połączenia jest łatwo penetrowana przez wodę obniżając żywotność połączenia uziomów, a tym samym całego uziomu do około 15-20 lat. W opozycji stoi tutaj połączenie skręcane, gdzie walcowany gwint pokryty miedzią przylega na długości kilku centymetrów pręta do złączki mosiężnej lub brązowej zabezpieczając skutecznie przed dopływem wody do odsłoniętej końcówki pręta (rys. 1).
Jeśli miedziowane uziemienia bezzłączkowe muszą być stosowane (np. ze względu na kilkunastoletnią planową żywotność uziemienia lub niewielką głębokość pogrążania), warto aby były to uziemienia kute, np. firmy KLK, które znacznie ograniczą występowanie opisanych wyżej wad. Najpewniejszym rozwiązaniem są jednak uziomy złączkowe, gwintowane.
Uziomy złączkowe gwintowane
W Polsce dostępne są uziemienia złączkowe gwintowane niewielu producentów. Jednym z nich jest firma Erico, której autoryzowanym dystrybutorem jest fhu Partner. Erico specjalizuje się w produkcji uziomów złączkowych pomiedziowanych o gwarantowanych powłokach minimum 254 mikrometrów. Odpowiednio dobrana stal, a także gama różnych długości jednostkowych uziomów i solidne złączki pozwalają pogrążać uziemienie do kilkudziesięciu metrów przy zachowaniu żywotności przez ponad 40 lat. Dzięki ustandaryzowaniu średnic nominalnych do 5/8 lub 3/4 cala, wraz z uziomami oferowana jest szeroka gama akcesoriów – złączy krzyżowych, zacisków z brązu armatniego, prefabrykowanych rozdzielników uziemień, pionowych przejść szczelnych, studzienek kontrolno-pomiarowych czy jednorazowych form do połączeń egzotermicznych. Elementy te pozwalają stworzyć bardzo rozbudowany system uziemiający w oparciu o kompatybilne i uzupełniające się rozwiązania.
Tańszą alternatywą do trudnych zastosowań są uziemienia fhu Partner ocynkowane ogniowo, o powłokach przekraczających 85 μm i średnicach 20 mm. Uziomy te wytwarzane są ze stali nie gorszej niż pomiedziowane, co jest o tyle istotne, że dla uziemień ocynkowanych polskie normy są mniej wymagające. Produkty te są stosowane np. na trudnych terenach przedgórskich.

Rys. 2. Połączenie egzotermiczne linek miedzianych w siatce uziomowej
Połączenia egzotermiczne
Ważną częścią systemu uziomowego są połączenia pomiędzy poszczególnymi elementami. Często punkty te, ze względu na niską jakość elementów łączących, stają się najsłabszymi ogniwami całego układu, decydując o jego trwałości. Aby zapewnić niemal niezniszczalne połączenie uziomu pionowego z pozostałą częścią systemu uziomowego, warto rozważyć wykorzystanie połączeń egzotermicznych (rys. 2). Połączenia takie cechują się bardzo dobrymi właściwościami elektrycznymi i mechanicznymi: są wytrzymałe, odporne na warunki środowiska i, co istotne, pozwalają swobodnie łączyć przewodniki miedziane (miedziowane) z ocynkowanymi, bez ryzyka powstania ogniwa galwanicznego.
Uziemienia aktywne i uziomy chemiczne
Poszukując metody na poprawę jakości przewodzenia do ziemi nie warto sięgać po takie rozwiązania jak uziemienia aktywne czy innego typu uziomy chemiczne. Przede wszystkim w ogromnej większości przypadków nie spełniają one norm PN-EN 62561-2 jako uziemienia pionowe. Co więcej substancje aktywne stanowiące ich komponent nie tylko nie spełniają normy PN-EN 62561-7, ale zawierają jawną wręcz informacje o szkodliwości, toksyczności czy innych działaniach drażniących. Tym samym produkty takie nie nadają się ani do użytku profesjonalnego ani przydomowego. Obecne trendy zakładają odejście od substancji aktywnie obniżających rezystancję uziemienia na rzecz naturalnych substancji mineralnych poprawiających uziemienie i, przede wszystkim, przebadanych na wydzielanie przewodzących jonów do wód gruntowych.

Rys. 3. Masa mineralna GEM:
a – wykonywanie ławy na bednarce miedzianej,
b – oblanie pionowego pręta uziomowego
Masa mineralna GEM
Taką naturalną i mineralną substancją jest GEM firmy Erico. Jest to rozwiązanie ponadstandardowe, często traktowane jak ostatnia możliwość osiągnięcia zakładanych przez system uziomowy parametrów. GEM po wyrobieniu ma konsystencję rzadkiego betonu (rys. 3), co pozwala tworzyć z niego ławy, wlewać go w otwory skalne, obudowywać uziemienia pionowe itp. Substancja po kilkudziesięciu godzinach krzepnie, staje się trudna do uszkodzenia i bardzo odporna na działanie wód gruntowych. GEM posiada wymagane atesty środowiskowe i jest w pełni zgodna z normą PN-EN 62561-7. Oporność masy GEM wynosi około 2 Ω na centymetr, co stanowi około 1% oporności standardowej masy bentonitowej.
GEM jest substancją trwałą, niewymagającą uzupełnień ani innych zabiegów w zakresie utrzymania. Sprawdza się w miejscach bardzo suchych, piaszczystych, żwirowych, kamienistych czy w przypadku litych skał, gdzie zwiększa efektywne pole oddawania prądów przewodnika do otoczenia. Sprawdza się również w przypadkach, gdy nie ma możliwości głębokiego pogrążania uziomów pionowych lub są wyraźne deficyty pola powierzchni działki pod zabudowę instalacji uziemiającej.

Rys. 4. Możliwe zastosowania masy mineralnej GEM:
a – budowa ław wokół poziomych przewodników uziemienia,
b – budowa walca okalającego uziemienia pionowe,
c – budowa uziemienia pionowego w odwiercie skalnym,
d – budowa uziemienia w naturalnej szczelinie skalnej w oparciu o giętką linkę
Zastosowania
Można wyróżnić cztery zastosowania masy mineralnej GEM:
• budowa ław wokół poziomych przewodników uziemienia (rys. 4a) – ława taka wylewana jest bezpośrednio na gruncie i najbardziej efektywny wynik (polepszenie rezystancji – ilość zużytej substancji) daje przy rozmiarach: na wysokość 2-3 cm pod i nad otaczanym przewodnikiem (co razem daje 4-6 cm wysokości) i na szerokość około 10 cm;
• budowa walca okalającego uziemienia pionowe (gdy np. nie ma możliwości głębokiego pogrążania uziomów pionowych – rys. 4b) – najlepiej wówczas sprawdza się wlewana do otworu o średnicach 7-25 cm otaczającego uziom;
• budowa uziemienia pionowego w odwiercie skalnym (rys. 4c), gdzie GEM pełni rolę przekaźnika pomiędzy uziomem prętowym a skałami otaczającymi uziom;
• budowa uziemienia w naturalnej szczelinie skalnej w oparciu o giętką linkę (np. miedzianą) zalaną GEM (rys. 4d) – masa szczelnie wypełnia przestrzenie międzyskalne i umożliwia skuteczne odprowadzanie prądów.
0Podsumowanie
Opisane wyżej rozwiązania mogą być wykorzystane zarówno w miejscach, gdzie występują trudne warunki glebowe lub hydrotechniczne, jak też przy niedoborze przestrzeni działki pod układanie instalacji uziemiejącej, a także podczas remontów instalacji obiektów przemysłowych, użyteczności publicznej i budynków mieszkalnych. Ważną cechą przedstawionych technologii jest trwałość zapewniająca długoletnią eksploatację, co jest nie tylko kategorią ekonomiczną ale przede wszystkim gwarantem właściwego poziomu bezpieczeństwa.
Rafał Budniok
Autor jest dyrektorem
firmy fhu Partner